Techmax 35: Carbon2Chem
plus Shipping Costs
Wie Abgase zu wertvollen Rohstoffen werden
2050 will Europa der erste klimaneutrale Kontinent sein und – gemäß des „Green New Deal“ der Europäischen Kommission (s. Geomax 29) – bereits bis zum Jahr 2030 die Netto-Treibhausgas-Emissionen um 55 Prozent gegenüber 1990 gesenkt haben. Das betrifft vor allem den Kohlenstoffdioxidausstoß, denn CO2 ist mit fast 90 Prozent mengenmäßig das bedeutendste klimaschädliche Gas. Um auf fossile Brennstoffe wie Kohle, Öl und Erdgas dann weitgehend verzichten zu können, muss vor allem die Industrie neue Wege gehen, sowohl für die Energieversorgung als auch für die Rohstoffbasis der chemischen Industrie. Eine gewaltige Herausforderung – für die es aber raffinierte Lösungen gibt. Zum Beispiel „Carbon2Chem“: Aus Abgas werde Rohstoff!
Im Jahr 2022 lag der Kohlenstoffdioxid-Anteil in der Luft bei rund 417 ppm und damit rund 40 Prozent höher als in vorindustrieller Zeit. Das Gas gehört zur natürlichen Atmosphäre der Erde, denn es entsteht seit Urzeiten als Nebenprodukt bei der Zellatmung der meisten Lebewesen, beim Zerfall toter Organismen und wird außerdem bei Vulkanausbrüchen freigesetzt. Den kontinuierlichen Ausstoß kompensieren Prozesse, die Kohlenstoffdioxid in großem Maßstab verbrauchen, wie die Fotosynthese von grünen Pflanzen und bestimmten Bakterienarten. Oder solche, die CO2 speichern, wie die Ozeane, Wälder und Moore es tun. Auch die Bildung von Erdöl, Erdgas und Kohle aus abgestorbenem organischem Material verringert den CO2-Gehalt der Erdatmosphäre. Doch durch die massenhafte Verbrennung dieser fossilen Energieträger wurde das sensible Gleichgewicht gestört. Und so steigt der CO2-Gehalt der Atmosphäre mit zunehmender Industrialisierung rund um den Globus stetig weiter an (s. Geomax 22).
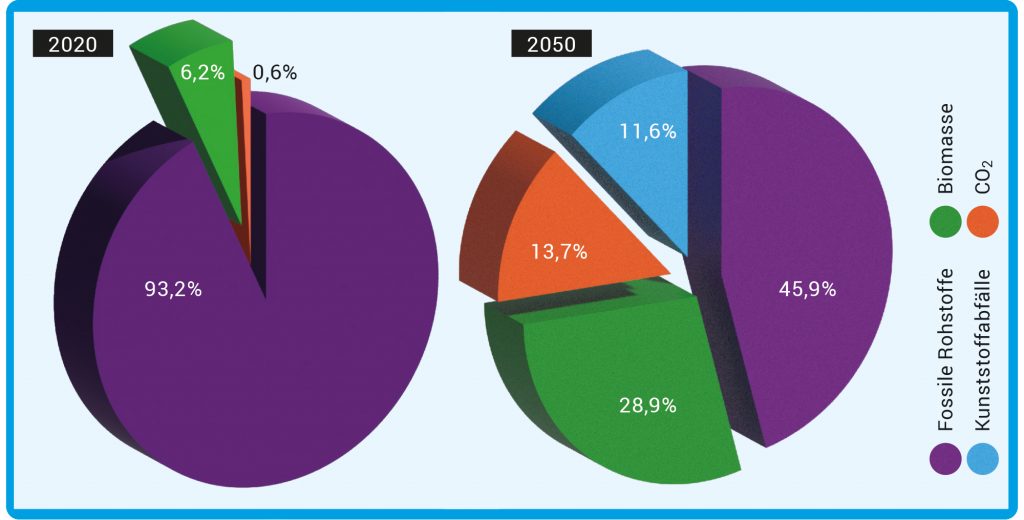
Abb. A: Mögliche Rohstoffbasis der Zukunft. Nach einer Modellrechnung könnte bis 2050 die Chemieindustrie in Deutschland 61 Prozent weniger Treibhausgase gegenüber 2020 freisetzen. Dafür ist mit einem rund vierfachen Strombedarf im Jahr 2050 zu rechnen. Nötig wären hohe Investitionen für neue Verfahren, und auch die Rohstoffbasis müsste massiv umgebaut werden: Biomasse, Kunststoffabfälle und CO2 müssten mehr als die Hälfte der fossile Rohstoffe ersetzen. Möglich wäre auch die Senkung der Emissionen auf nahe Null – mit einem entsprechend höheren Bedarf an Strom usw.. Zur Vergleichbarkeit der verschiedenen Rohstoffe werden in den Diagrammen die eingesetzten Mengen auf den Kohlenstoffgehalt bezogen.
© Quelle: DECHEMA & FutureCamp: ROADMAP CHEMIE 2050. 2019, S. 76. ISBN: 978-3-89746-223-6
In Deutschland sind seit 1990 die Treibhausgasemissionen fast kontinuierlich um 46 Prozent gesunken: von 1.251 auf 674 Millionen Tonnen pro Jahr. Nach der Energiewirtschaft hat die Industrie den zweitgrößten Anteil daran. Vor allem zwischen 2018 und 2023 war ein deutlicher Rückgang zu verzeichnen – bedingt durch den geringeren Einsatz fossiler Brennstoffe, insbesondere von Erdgas und Steinkohle. Doch das reicht bei weitem nicht aus. Zudem beruht die Rohstoffbasis der chemischen Industrie noch immer zu über 90 Prozent auf fossilen Quellen, was sich für eine deutliche Reduktion der Treibhausgase bis 2050 drastisch ändern müsste (Abb. A).
Ließe sich das eine nicht mit dem anderen kompensieren? Industriell anfallendes klimaschädliches CO2 als Quelle für Rohstoffe nutzen und somit in die Wertschöpfungskette zurückführen? Genau das wird im Rahmen von Carbon2Chem erforscht – einem Grundstein künftiger „Carbon Capture and Use Technologien“ (CCU). Carbon2Chem ist ein Verbundprojekt des Stahlkonzerns thyssenkrupp, des Max-Planck-Instituts für Chemische Energiekonversion sowie des Fraunhofer-Instituts für Umwelt-, Sicherheits- und Energietechnik und 14 weiteren Partnern. In der Pilotanlage auf dem Gelände des größten Stahlwerks Europas in Duisburg filtern die Forschenden aus den Hochofenabgasen Kohlenstoffmonoxid und -dioxid heraus, führen es mit Wasserstoff zusammen und erzeugen in einer katalytischen Reaktion daraus Methanol.
Ein Klassiker für die Transformation
Warum gerade Methanol? Das hat mehrere Gründe. Zum einen lassen sich aus dem kleinsten Alkoholmolekül leicht weitere chemische Grundstoffe herstellen. Zum anderen kann Methanol direkt als Kraftstoff genutzt werden. Nicht nur für Autos, wie etwa in Brasilien, sondern auch für Mobilität in Bereichen, in denen Elektroantriebe noch keine Alternative sind – zum Beispiel bei XXL-Containerschiffen. Die 350 Meter lange, 45 Meter breite und 60.000 PS starke „Ane Maersk“ hat Platz für 16.600 Container und ist das erste Schiff ihrer Art, das nun mit grünem Methanol statt mit umweltschädlichem Schweröl über die Ozeane fährt.
Für Forschende wie Holger Ruland vom Max-Planck-Institut für Chemische Energiekonversion hat der Alkohol einen weiteren Pluspunkt, denn kaum ein katalytisches Verfahren ist so gut untersucht wie die Methanolsynthese. Bereits 1923 gelang es dem Chemiker Matthias Piers, den Alkohol großtechnisch aus Synthesegas (CO + H2) im Hochdruckverfahren an Zinkoxid-Chromoxid-Katalysatoren herzustellen. Noch heute gehört dies zu den „Top Five“ der katalytischen Verfahren. Bisher wurde das Synthesegas dafür durch Kohlevergasung oder aus Erdgas gewonnen. „Man kennt also die Gaszusammensetzung recht gut und weiß, wie man es aufreinigen muss. Auch an den Katalysatoren wurde inzwischen viel optimiert“, sagt Ruland, der nun Kupfer-Zink-Katalysatoren dafür einsetzt.
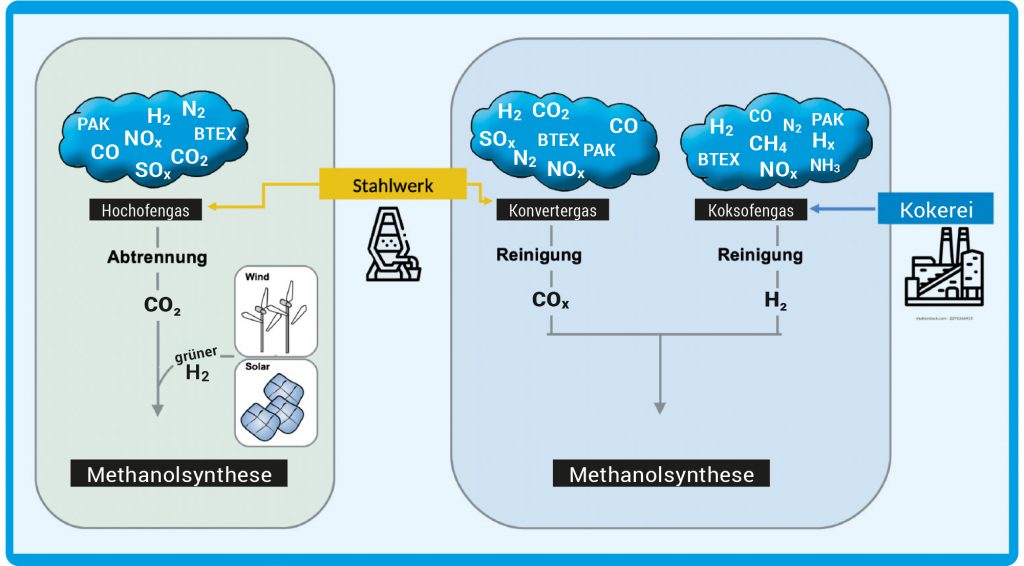
Abb. B: Möglichkeiten der Abgasverwertung. Links: Hochofengas enthält von allen Abgasen die höchste CO2-Menge. Das CO2 muss abgetrennt und danach mit H2 angereichert werden. Rechts: CO-reiches Konvertergas und H2-reiches Koksofengas werden gereinigt und gemischt. Die größte Herausforderung dabei sind Spurengase, die den Katalysator schädigen können. Die Erzeugung des H2 sollte mit erneuerbaren Energiequellen erfolgen, um eine positive Kohlenstoffbilanz zu erhalten. (BTEX: Benzol, Toluol, Ethylbenzol, Xylole. PAK: polyzyklische aromatische Kohlenwasserstoffe)
© Verändert nach Chem. Ing. Tech. 2018, 1419 ff. / https://doi.org/10.1002/cite.201800017 / CC BY-NC 4.0
Die heißen Abgase aus dem Stahlwerk in Duisburg (s. Titelbild) dürfen natürlich schon heute nicht mehr einfach in die Luft geblasen werden. Das wäre im Grunde auch Verschwendung. Durch ein verzweigtes System aus zum Teil mannshohen Rohren werden sie über das Werksgelände geleitet, zum Teil in den Prozess direkt wieder eingespeist, weil sie noch viel Kohlenstoffmonoxid und Wasserstoff enthalten. Alle anderen Gase werden herausgefiltert und zum werkseigenen Gaskraftwerk geleitet, wo sie final verbrannt werden – um Strom für das Werksgelände zu erzeugen. Für das Carbon2Chem-Pilotprojekt wird das wertvolle Gasgemisch (Hochofengas, s. Abb. B) aber direkt hinter dem Hochofen abgezwackt. Neben CO, CO2 und H2 enthält es etliche Kohlenwasserstoffe, Stickstoff und Ammoniak. Mehr als 500 Verbindungen insgesamt, viele davon nur im niedrigen ppb-Bereich und noch längst nicht alle sind analysiert. Was genau drin ist, hängt davon ab, welches Erz und welche Kohle zur Stahlherstellung verwendet wird. Damit die Methanol-Produktion später einmal in großem Maßstab und kontinuierlich laufen kann, ist es notwendig zu wissen, welche Verbindungen man unbedingt vorher herausfiltern muss, damit der Katalysator nicht streikt. Denn im Idealfall sollte seine Aktivität über mehrere Jahre nicht nachlassen. „Mehr als 100 ppb Schwefel – in welcher Form auch immer – machen Probleme, denn das Element setzt sich auf die Kupfer-Zink-Grenzflächen und vergiftet so den Katalysator“, erklärt Ruland. Die Oberfläche des Kats verliert dadurch die aktiven Zentren, an denen die Synthese stattfinden kann.
Empfindliches Gleichgewicht
Für die Methanolsynthese können Gemische aus CO und CO2 eingesetzt werden, da beide Kohlenstoffoxide mit Wasserstoff in einer exothermen Reaktion den Alkohol bilden (Abb. C). Nach dem Prinzip von Le Chatelier lässt sich das Gleichgewicht durch Optimierung von Druck und Temperatur zugunsten des Produktes weit nach rechts verschieben. „Bei den üblichen kupferbasierten Katalysatoren geht das am besten bei 50 bis 100 bar und 240 bis 260 °C. Doch je mehr CO2 im Gasgemisch ist, desto ungünstiger ist es für das thermodynamische Gleichgewicht“, sagt Ruland (s. Erklärung in Abb. C). Man erhält also etwas weniger Methanol pro Reaktor-Durchgang, was aber durch Rückführung der Gase in den Prozess wieder ausgeglichen werden kann. Unter optimalen Bedingungen entsteht dann zu 99 Prozent reines Methanol, das zum Abschluss, je nach gewünschtem Reinheitsgrad, ein- oder zweimal destilliert wird.
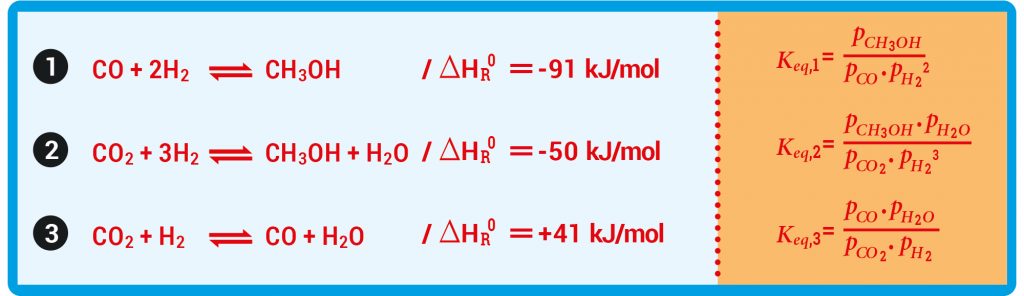
Abb. C: Herstellung von Methanol aus Synthesegas Methanol wird im Wesentlichen aus CO2 gebildet, da die Hydrierung von CO2 viel schneller abläuft als von CO. Die Reaktionen (1) und (2) sind durch die Reaktion (3) gekoppelt, die ebenfalls stattfindet und katalysiert wird. Die Hinreaktionen sind in den Gleichungen 1 und 2 exotherm, in Gleichung 3 endotherm. Temperaturerniedrigung und Druckerhöhung begünstigen in den Reaktionen (1) und (2) die Methanolbildung. Da alle drei Reaktionen des Reaktionsnetzwerkes die Gleichgewichtslage beeinflussen, spielt auch die Reaktion (3) eine wichtige Rolle: Je mehr CO2 im Gas enthalten ist, desto mehr Wasser wird über die Reaktion (3) gebildet und verringert dadurch entsprechend der Gleichgewichtskonstante Keq,2 noch zusätzlich den im Gleichgewicht möglichen Methanolanteil. Ein höherer CO-Anteil im Gas hat den gegenteiligen Effekt. (pi: Partialdruck der Komponente i)
© MPG // HNBM
Für die Stahlherstellung wird Eisenerz, ein Gemenge von Eisenoxiden (Magnetit und Hämatit) und -carbonat (Siderit), zunächst zu einem Sinterkuchen „verbacken“ und dann in grobe Stücke zerbrochen. Zeitgleich wird in der Kokerei Kohle in Koks, also fast Hochofengas reinen Kohlenstoff, umgewandelt. Dabei entsteht das Koksofengas, was zusammen mit dem Konvertergas für die Methanolsynthese verwendet werden kann (s. Abb. B). Koks dient später im Hochofen zusammen mit Kohlenstoffmonoxid als Reduktionsmittel für die Eisenoxide. Im Rahmen der grünen Transformation sollen dieser Prozess, der extrem viel CO2 erzeugt, sowie die Energieversorgung der Stahlwerke baldmöglichst durch Direktreduktion mittels grünem Wasserstoff ersetzt werden. Auch wenn die Stahlherstellung irgendwann beinahe „grün“ sein wird, macht es trotzdem Sinn, Carbon2Chem hier zu erproben und anzuwenden. Denn es gibt es noch einen zweiten Prozess beim „Stahlkochen“: Wenn das Roheisen mit Stahlschrott verschmolzen wird – in der sogenannten Konverter-Route – wird ebenfalls CO2 freigesetzt, wenn auch weit weniger. Und dieser Anteil wird sich nicht vermeiden lassen.
Kohlenstoff für Basischemikalien
Aus Synthesegas lassen sich nicht nur Methanol herstellen, sondern auch höhere Alkohole und beispielsweise auch Methan – mit Hilfe von Nickelkatalysatoren. Das ist quasi „nachhaltiges“ Erdgas. Klar kann man das zur Energiegewinnung einfach „verheizen“, was nicht sonderlich klimafreundlich wäre. Methan ist jedoch, ebenso wie Wasserstoff, auch ein möglicher Zwischenspeicher für erneuerbare Energien. Über die Fischer-Tropsch-Synthese sind zudem langkettige Kohlenwasserstoffe zugänglich: Alkane und Alkene, die für die Kunststoffindustrie interessant sind. Und Oxomethylenether, eine Art Dieselderivat, das aber rußfrei verbrennt.
Das Hochofengas enthält neben CO2 auch etwa 50 Prozent Stickstoff. Auch der lässt sich nutzen und mit Wasserstoff im Haber-Bosch-Verfahren zu Ammoniak umsetzen, einem weiteren begehrten Grundstoff (s. Techmax 10). „Das passt zwar auf den ersten Blick nicht zum Carbon2Chem-Gedanken. Aber Ammoniak wird mit Kohlenstoffdioxid weiter zu Harnstoff umgesetzt, und so erzielt man dann auch einen CO2-Minderungseffekt“, erklärt Holger Ruland. 80 Prozent der weltweiten Ammoniakproduktion werden in Salpetersäure umgewandelt. „Ohne die daraus erzeugten Düngemittel hätte sich die Weltbevölkerung nicht so rasant entwickeln können, weil nicht ausreichend Nahrungsmittel zur Verfügung gestanden hätten“, sagt Holger Ruland.
Wenn der Hochofen durch Direktreduktion ersetzt wird, ändert sich natürlich die Gasverfügbarkeit am Stahlwerk. „Wir müssen deshalb für die Übergangsperioden gut planen, um dann noch wirtschaftlich Methanol am Standort erzeugen zu können.“ Ob es rentabel ist, wird letztlich auch davon abhängen, wieviel überschüssiger Strom aus Solar- und Windkraftanlagen, der nicht gespeichert werden kann, pro Jahr zur Verfügung stehen wird. „Ein industrieller Prozess läuft üblicherweise 8.000 Stunden pro Jahr kontinuierlich. Das wird in einem erneuerbaren System so sicher nicht möglich sein. Sind es aber nur 1.000 Stunden, wäre das unwirtschaftlich.“ Teilweise ließe sich das über Zwischenspeicher abpuffern. Sprich: Indem man den Überschussstrom schon mal nutzt, um grünen Wasserstoff auf Vorrat zu produzieren. Denn Strom, der aus Kohle oder Erdgas kommt, für die Methanolsynthese zu verwenden, wäre nicht nachhaltig und der Kohlenstoffkreislauf wäre nicht geschlossen.
Die Pilotanlage in Duisburg erzeugt pro Tag bereits 50 Liter Methanol. Demnächst soll ein Scale-up in eine größere Anlage erfolgen, die schon im Tonnen-Maßstab arbeiten wird. Und wenn alles gut läuft, könnte das Verfahren vielleicht schon in fünf Jahren industriell eingesetzt werden. Damit ließe sich, wie Holger Ruland meint, der Methanol-Markt „regelrecht fluten“. Vorausgesetzt natürlich, der Preis für das Produkt stimmt! Und der hängt unter anderem davon ab, wie teuer der grüne Wasserstoff für die Herstellung des Methanols ist und wie hoch die CO2-Abgabe sein wird, die nicht nachhaltige Produkte verteuert. Ein ebenso komplexes wie hochpolitisches Thema.
Gute Gründe für Optimismus
Dass es für Umweltprobleme gute Lösungen gibt, zeigt ein Blick in die jüngere Vergangenheit. Gesundheitsschädliche Schwefelgase, die bei der Verbrennung von Kohle und Müll entstehen, werden seit 1983 durch Rauchgas-Entschwefelungsanlagen (REA) aus den Abgasen von Kraftwerken und Müllverbrennungsanlagen herausgewaschen und in Calciumsulfat umgewandelt. Dieser REA-Gips deckt den Gipsbedarf der Baubranche derzeit zu 40 Prozent. „Sulfur Capture and Use“ sozusagen, lange bevor es den Begriff gab. Zweites Beispiel: Das Ozonloch. 1985 wurde es erstmals über dem Südpol entdeckt und bereits zwei Jahre später die Ursache dafür erkannt. Bereits 1987 unterzeichneten 197 Staaten das Montreal-Protokoll und verpflichteten sich, Produktion und Verbrauch der acht wichtigsten Fluor-Chlor-Kohlenwasserstoffe (FCKW) drastisch zu reduzieren. Inzwischen verkleinert sich das Ozonloch über der Antarktis merklich und Forschende gehen davon aus, dass es in 50 bis 100 Jahren wieder ganz geschlossen sein wird.
Den Kreislauf schließen
„In beiden Fällen waren die Verursacher punktuell und deshalb auch gut abzustellen. Das Zuviel an Kohlenstoffdioxid entsteht jedoch überall“, betont Holger Ruland. „Deshalb wird ein vielfältiger Mix von Technologien nötig sein, um CO2 sowohl zu vermeiden, als auch zu verwerten und zu lagern.“ Auch Carbon Capture and Storage (CCS) wird aus seiner Sicht Teil der Lösung sein. „Vor allem an Standorten, an denen es keine Industrieansiedlungen gibt, die das Gas nutzen könnten, macht es Sinn, es zu verflüssigen und in unterirdische Kavernen zu pumpen. Am besten dort, wo man früher Erdgas herausgeholt hat.“
CCU-Technologien voranzutreiben, meint Ruland, werde gerade in der Übergangszeit wichtig sein, bis es tatsächlich gelingt, einen geschlossenen Kreislauf herzustellen. In dieser Phase gilt es, alle anderen chemischen Verfahren, die jetzt noch auf fossilen Rohstoffen basieren, zu prüfen und umzustellen, um die Kohlenstoffverwertungskette wirklich nachhaltig zu machen. Auf lange Sicht wird man auch um Direct Air Capture (DAC) nicht herum kommen. Auch wenn es aktuell noch nicht wirklich rentabel ist. Ein kniffliges Problem: Zwar führen 417 ppm schon jetzt zu dramatischen Klimaveränderungen auf der Erde. Neben 78,08 Prozent Stickstoff, 20,95 Prozent Sauerstoff und rund einem Prozent an Edelgasen und anderen, wirken die 0,04 Prozent Kohlenstoffdioxid jedoch wie ein „Spurenelement“. Und dies über Absorber aus dem Gasgemisch gezielt herauszufischen, ist eine technische Herausforderung. Aber keine unlösbare! In Island wurde im Mai 2024 „Mammoth“, die weltweit größte Anlage für Direct Air Capture and Storage (DAC+S) in Betrieb genommen. Der „CO2-Sauger“ des Schweizer Unternehmens Climeworks, das aus einem Spin-off der Eidgenössischen Hochschule Zürich entstanden ist, soll pro Jahr 36.000 Tonnen Kohlenstoffdioxid aus der Luft filtern und unterirdisch speichern. Der Strom für die sehr energieintensive Anlage wird übrigens zu 100 Prozent „grün“ erzeugt – durch Geothermie.
Das Carbon2Chem-Verfahren soll natürlich auch in anderen CO2-intensiven Industriezweigen angewendet werden – zum Beispiel bei der Zementherstellung oder der Müllverbrennung. Letztere wird nie aufhören, auch wenn die Menge der Abfälle, in Deutschland 2023 erstmals knapp unter die 400-Millionen-Tonnen-Marke fiel. 82 Prozent davon werden übrigens bereits jetzt „stofflich oder energetisch verwertet“. Sprich: recycelt oder verbrannt und die Abwärme für Fernwärme oder zur Stromerzeugung genutzt. Da Plastikmüll zum größten Teil aus Kohlenstoff besteht und deshalb ein wertvoller Rohstoff ist, wird auch an Verfahren für das chemische Recycling geforscht, um nicht-sortenreine Kunststoffabfälle wiederzuverwerten. Bis diese Verfahren im großen Maßstab angewendet werden können, wäre es aber auch schon ein nachhaltigerer Weg, „Plastikmüll zur Energieerzeugung zu verbrennen und das entstehende CO2 einzufangen und mit Hilfe von Carbon2Chem umzuwandeln“, sagt Holger Ruland.
Abbildungshinweise:
Titelbild © thyssenkrupp Steel Europe AG
Abb. A: © Quelle: DECHEMA & FutureCamp: ROADMAP CHEMIE 2050. 2019, S. 76. ISBN: 978-3-89746-223-6
Abb. B: © Verändert nach Chem. Ing. Tech. 2018, 1419 ff. / https://doi.org/10.1002/cite.201800017 / CC BY-NC 4.0
Abb. C: © MPG //HNBM
Der Text wird unter CC BY-NC-SA 4.0 veröffentlicht.
TECHMAX Ausgabe 35, Juli 2024; Text: Dr. Catarina Pietschmann; Redaktion: Dr. Tanja Fendt