Techmax 19: Keine Chance für den Rost
plus Shipping Costs
Wie Forschung Korrosionsschutz entwickelt
Genua, 14. August 2018: Kurz nach halb zwölf bricht die Morandi-Brücke zusammen. Autos und Lastwagen stürzen in die Tiefe, es gibt 43 Tote. Der Grund für das Unglück: Korrosion. Eine völlig durchgerostete Stahltrosse war gerissen. Gutachten gehen davon aus, dass die Brücke über Jahre mangelhaft gewartet worden war. Korrosion kann Menschenleben kosten. Und sie richtet auch enorme wirtschaftliche Schäden an – weltweit. Denn überall, nicht nur in Brücken, sondern auch in Gebäuden, Containern, Schiffen, Autos und Flugzeugen steckt Stahl. Beginnt er zu rosten, werden teure Reparaturen fällig. Korrosion verschlingt jährlich geschätzt 3 bis 4 Prozent des Bruttoinlandsprodukts von Industriestaaten.
Doch was passiert bei der Korrosion des Stahls? Dieser besteht vorwiegend aus Eisen, und als unedles Metall reagiert Eisen leicht mit Stoffen in der Umgebung. So oxidiert es mit Sauerstoff in Gegenwart von Wasser und es entsteht dabei Eisen(II)-hydroxid. In einer weiteren Reaktion oxidiert das Eisen(II)-hydroxid dann zu Eisen(III)-hydroxid: Der rotbraune Rost wird sichtbar. Nach und nach wird immer mehr Eisen in Eisen(III)-hydroxid umgewandelt. So frisst sich der Rost langsam durch das Metall hindurch. Die Korrosion hat ihr Zerstörungswerk begonnen.
Wie lässt sich Stahl vor seinem größten Feind schützen? Kunststoffbeschichtungen können zum Beispiel verhindern, dass das Eisen in Kontakt mit den Stoffen in seiner Umgebung kommt. Oder Zink liegt als Schutz vor Korrosion über dem Stahl. Als unedleres Metall oxidiert Zink zuerst und „opfert“ sich so für das Eisen, bis die Zinkschicht irgendwann aufgebraucht ist. Wissenschaftlerinnen und Wissenschaftler suchen nach neuen Wegen, Stahl vor Rost zu schützen. Zum Beispiel gibt es den amorphen Stahl, der wegen seiner Nanostruktur weniger korrosionsanfällig ist. Und es gibt den Ansatz, neuartige Beschichtungen zu entwickeln, die eine beginnende Korrosion an beschädigten Stellen stoppen und sich dann selbst reparieren. Solche intelligenten, selbstheilenden Schutzschichten müssen bestimmte Voraussetzungen erfüllen. Sie sollen Inhibitoren – Wirkstoffe, die die Korrosion stoppen – speichern und erst dann freisetzen, wenn die Beschichtung beschädigt ist und das darunter liegende Metall angegriffen wird. Dafür braucht es ein zuverlässiges Trigger-Signal sowie einen Mechanismus, der den Transport der Wirkstoffe zum Defekt sicherstellt. Werden die kleinen Korrosionsbekämpfer schließlich nicht mehr gebraucht, weil das Problem behoben ist, soll die Freisetzung wieder beendet werden. Der Clou zum Schluss: Die Beschichtung verschließt ihre Verletzungen mit eigenen Hilfsmitteln. Sie heilt sich selbst. Gesucht wird also eine Art „Wunder-Beschichtung“.
Leitende Kunststoffe
Michael Rohwerder, Leiter der Forschungsgruppe Korrosion am Max-Planck-Institut für Eisenforschung in Düsseldorf, befasst sich seit gut 20 Jahren mit intelligenten selbstheilenden Beschichtungen. Er interessiert sich dabei vor allem für selbstständig leitfähige Polymere wie Polyanilin und Polypyrrol. Solche Polymere besitzen konjugierte Doppelbindungen und leiten ähnlich gut wie Metalle. Sie verhalten sich damit konträr zu den meisten Kunststoffen, die Nichtleiter sind. Die Leitfähigkeit ist über Oxidation und Reduktion reversibel veränderbar: Polypyrrol kann vom reduzierten (nicht-leitenden) Zustand in den halb-oxidierten (leitenden) Zustand und wieder zurück wechseln (Abb. A). Diese Eigenschaften machte sich Rohwerder für die Entwicklung intelligenter selbstheilender Beschichtungen zunutze. Seine Grundidee war dabei von Anfang an: Das Trigger-Signal, das die Freisetzung des Inhibitors einleitet, soll ein Vorgang sein, den Korrosion immer verursacht: das Sinken des Elektrodenpotenzials im Metall, wenn die Korrosion beginnt. Genau dafür sind elektrisch leitende Polymere ideal, weil sie wegen ihrer Leitfähigkeit auf dieses Signal reagieren.
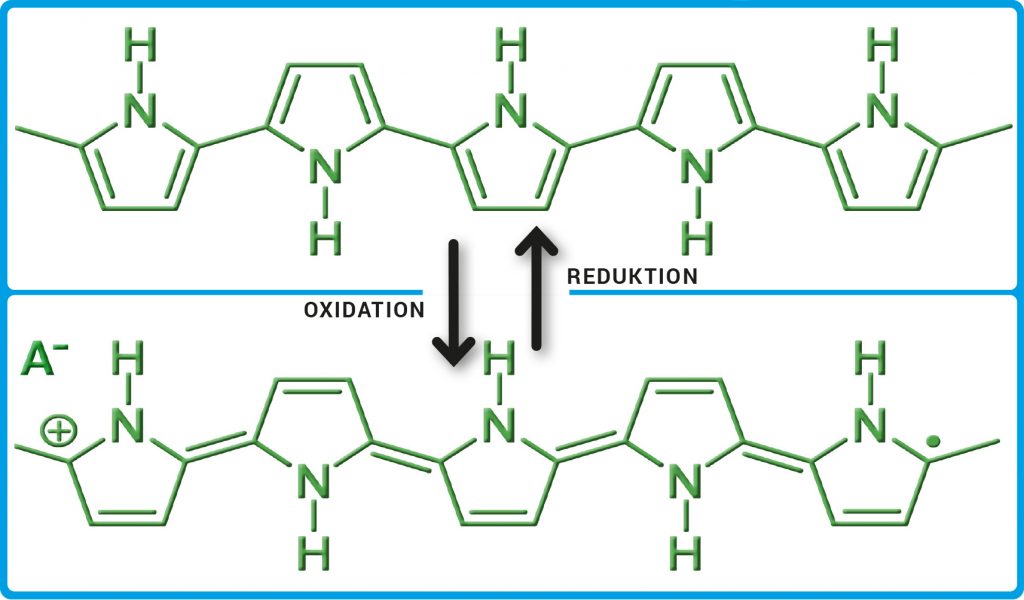
Abb. A: Polypyrrol. Die Abbildung zeigt Ausschnitte aus dem Polymer. Bei der Oxidation werden dem Polypyrrol Elektronen entzogen und positive Ladungen erzeugt. Für den notwendigen Ladungsausgleich sorgen eingelagerte Anionen (A–). Im halb-oxidierten Zustand (unten) ist das Polypyrrol leitend. In der reduzierten Form (oben) ist es nicht-leitend.
© MPG // HNBM-design.de // CC BY-NC-SA 4.0
Smarte Verpackung
Für die Entwicklung einer intelligenten Beschichtung musste im ersten Schritt der Inhibitor in der Schutzschicht gespeichert werden, erst bei Korrosion des darunterliegenden Metalls sollte er freigesetzt werden. In sämtlichen Versuchsreihen, vom Start im Jahr 2002 bis heute, wurde als korrodierende Metallschicht Zink verwendet, weil in der industriellen Fertigung für hochwertige Anwendungen auch meist eine Zinkschicht über dem Stahl liegt. Zuerst testete Rohwerder einen negativ geladenen Inhibitor. Die Teilchen waren als Gegenionen zur positiven Ladung des leitfähigen Polymers direkt in der Schicht eingelagert. Aber es klappte nicht so richtig, da die Inhibitor-Teilchen in zu geringen Mengen freigesetzt wurden. Einen neuen Ansatz für die Speicherung fand Rohwerder in den späteren Versuchen ab 2010. Die Inhibitor-Teilchen wurden nun in Kapseln mit Hüllen aus leitfähigem Polymer eingebettet. „In Kapseln lässt sich bei gleichem Volumen mehr davon speichern als direkt in der Polymerschicht“, erklärt Rohwerder den Vorteil der Kapsel-Methode. „Direkt im Polymergerüst sind die Inhibitor-Teilchen ja nur als Gegenionen zur positiven Ladung gespeichert, was einen kleinen Volumenanteil ausmacht. Im Kapselinneren dagegen können sie das ganze verfügbare Volumen einnehmen.“
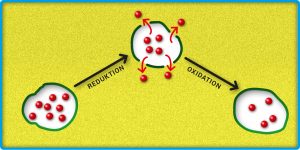
Abb. B: Wiederverschließbare Behälter. Die Kapselwände (grün) bestehen aus leitfähigem Polymer. Durch Reduktion werden diese porös und die Inhibitor-Teilchen (rote Kugeln) verlassen die Kapsel. Erfolgt eine Rückoxidation des Polymers, schließen sich die Poren in der Kapselwand wieder.
© MPG // HNBM-design.de // CC BY-NC-SA 4.0
Als nächstes untersuchte Rohwerder die Freisetzung der Wirkstoffe. Bei den Experimenten wurde in die Polymerschicht bis zur Zinkschicht hineingeschnitten und etwas Salzlösung auf die offene Stelle getropft. Durch die beginnende Korrosion an der Zinkschicht sinkt das Elektrodenpotenzial und breitet sich aus. Die Kapselwände aus leitfähigem Polymer werden reduziert und hydrophiler. Die Kapseln nehmen bei dem Vorgang Kationen und Wassermoleküle aus der Salzlösung auf, die aus dem Defekt herüberströmen. In der Folge nimmt das Volumen der Kapseln zu, die Wände werden porös und durchlässig, so dass die Inhibitor-Teilchen freigesetzt werden (Abb. B). Der erste große Durchbruch.
Schnellstraße für Teilchen
Jetzt ließen sich die Wirkstoffe sicher in den Kapseln speichern, sogar in ausreichend großen Mengen. Und es gab ein Trigger-Signal, das sich vom Defekt im Zink über die Polymerschicht zu den Kapseln ausbreitete, wodurch die Wirkstoffe freigesetzt wurden. Aber damit war der Anti-Korrosions-Mechanismus noch nicht komplett. In der aktuellen Forschungsphase geht es nun darum, den Transport der Wirkstoffe sicherzustellen und möglichst noch zu beschleunigen. Zuerst der Transport selbst: Wie gelangen die Inhibitor-Teilchen durch die Polymerschicht zum Defekt im Zink, nachdem sie aus den Kapseln freigesetzt worden sind? Durch Reduktion wird die Polymerschicht, genau wie die Kapselwände, hydrophil und erleichtert damit den Transport der Inhibitor-Teilchen. Dieser erfolgt vor allem durch Diffusion. Die freigesetzten Wirkstoff-Teilchen diffundieren entlang eines Konzentrationsgefälles. Auf diese Weise gelangen sie vom Ort ihrer Freisetzung, an dem eine hohe Teilchenkonzentration vorliegt, bis zur Korrosionsstelle (Abb. C). Haben die Inhibitor-Teilchen der Korrosion Einhalt geboten, steigt das Elektrodenpotenzial im Defekt wieder an, da das Zink passiviert wird. Das führt zu einer Rückoxidation der Polymerschicht und der Kapselwände mit Luftsauerstoff. Die porösen Kapselwände schließen sich wieder.
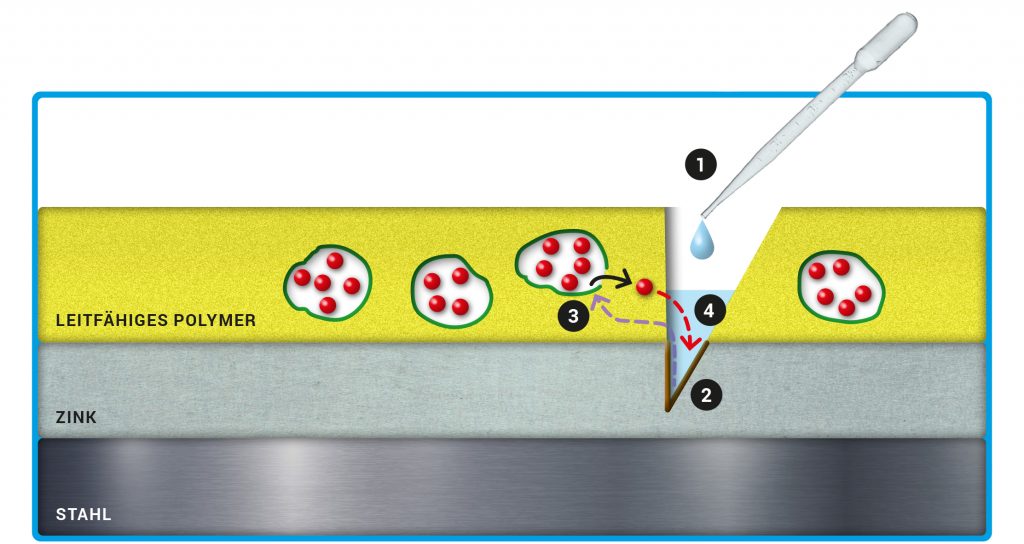
Abb. C: Selbstheilende Schicht. In der Schutzschicht aus leitfähigem Polypyrrol (gelb) stecken Kapseln, deren Wände (grün) aus leitfähigem Polyanilin bestehen. Die Kapsel enthalten die Inhibitor-Teilchen (rote Kugeln). In vielen Arbeiten wurde 3-Nitrosalicylat verwendet, das gut auf Zink wirkt. Unter der Polymerschicht liegt die Zinkschicht. Bei den Experimenten wird in die obere Beschichtung hineingeschnitten und etwas Salzlösung auf die offene Stelle getropft (1). So beginnt das Zink unter dem Schnitt zu korrodieren (2). Dadurch sinkt das Elektrodenpotenzial – das entscheidende Trigger-Signal, welches sich vom Defekt im Zink bis zur Polymerschicht und den darin eingebetteten Kapseln ausbreitet (3). Die Kapseln nehmen Kationen und Wassermoleküle auf, die Kapselwände werden porös und durchlässig. Die freigesetzten Inhibitor-Teilchen diffundieren anschließend zum Defekt (4).
© MPG // HNBM-design.de // CC BY-NC-SA 4.0
Auch die Frage, wie beim Transport das nötige Tempo erreicht wird, ließ sich in den jüngsten Versuchen klären. Bei einem leitfähigen Polymer ist die Beweglichkeit der Inhibitor-Teilchen in der Schicht zunächst eingeschränkt. Sie erhöht sich aber stark, sobald das Polymer reduziert wird und Wassermoleküle aufnimmt. Über die Reduktion wird die Polymerschicht gleichsam von Tempo-30-Zone auf Schnellstraße geschaltet. „Der Trigger, das absinkende Elektrodenpotenzial, bewirkt also nicht nur die Freisetzung der Inhibitor-Teilchen aus den im Polymer eingelagerten Kapseln, sondern auch deren zügigen Transport“, fasst Rohwerder zusammen. Damit hat er den nächsten Durchbruch geschafft.
Wie eine neue Haut entsteht
Und wie steht es um die Selbstheilung der Beschichtung als krönender Abschluss? Auch daran arbeitet Rohwerder zur Zeit. „Das Bilden einer neuen Polymerhaut ist keine ganz einfache Sache.“ Eine Möglichkeit besteht darin, Monomere zu polymerisieren. Diese können auch gut in leitfähigen Polymerkapseln gespeichert und auf das Trigger-Signal hin freigesetzt werden. Jedoch benötigt die Polymerisierung noch einen Katalysator. Die Katalysator-Teilchen sind allerdings durch die Einkapselung nicht gut genug geschützt vor Wasser und Sauerstoff. „Sie würden schon nach wenigen Tagen oder Wochen oxidiert werden“, sagt Rohwerder. Daher hat er sich einen Trick ausgedacht: Die Kapseln mit den Katalysator-Teilchen werden nicht in der Polymerschicht gespeichert, sondern in der Zinkschicht darunter. Beginnt dann die Korrosion, werden die Katalysator-Teilchen freigesetzt und ermöglichen die Polymerisierung der ebenfalls freiwerdenden Monomere. So bildet sich direkt an der defekten Stelle neues Polymer. Wie bei uns Menschen, wenn wir uns in den Finger geschnitten haben und die Wunde langsam wieder heilt, indem sich am Schnitt neue Haut bildet.
Ein Leuchten, das Korrosion verrät
Auch für das Aufspüren von Defekten lässt sich ein cleverer Mechanismus in der Polymerschicht nutzen. Mit Sensoren aus organischen Kohlenstoffverbindungen, welche in porösen, nicht leitfähigen Siliziumdioxidkapseln in der Beschichtung stecken. Sie machen Korrosion sichtbar, indem die betroffenen Stellen zu glimmen beginnen, wenn der Stahl von außen mit UV-Licht bestrahlt wird. „Solche Sensoren würden Überprüfungen viel einfacher machen, weil sich die Korrosion schon nachweisen ließe, bevor sie mit bloßem Auge sichtbar wird“, sagt Rohwerder. Sonst wird Korrosion erst im fortgeschrittenen Stadium erkannt, wenn sich schon Blasen im Lack gebildet haben oder rötliche Rostverfärbungen zu sehen sind. Bei sehr dicken Beschichtungen wird bei Kontrollen sogar die Beschichtung entfernt, um zu schauen, wie es darunter aussieht. Mit den eingebauten Sensoren wäre das nicht mehr nötig.
Was da in Düsseldorf passiert, ist Grundlagenforschung. Sie schafft die Voraussetzungen, dass intelligente Beschichtungen in der Zukunft bei Brücken und Schiffen zur Anwendung kommen können. Stabil funktionierende Lösungen zu finden, erfordert eine Menge Zeit und noch mehr Ausdauer, weil sich Ansätze, die zuerst vielversprechend erscheinen, manchmal als falsch erweisen. Dann heißt es: Die Erfahrungen mitnehmen und neue Ideen ausprobieren. Diese „Umwege“ gehören zur Grundlagenforschung dazu und führen letztlich zu Fortschritten oder gar Durchbrüchen. Rohwerder ist mit dem bisher Erreichten zufrieden: „Es sind sicher noch Verbesserungen nötig, etwa für das erfolgreiche Verschließen großer Defekte. Auch muss die Beschichtung ja zehn Jahre oder länger halten und darf nicht zu teuer sein. Aber wir kommen dem Ziel, völlig neuartige selbstheilende Beschichtungen zu entwickeln, immer näher.“
Pluspunkt für das Klima
Zwar gibt es schon Beschichtungen auf dem Markt, die als selbstheilend bezeichnet werden. Aber diese haben große Schwächen, zum Beispiel brauchen sie Wärme zum Selbstheilen. „Was wir vorschlagen, sind weitreichende Neuerungen. Die gibt es noch gar nicht.“ Und es wird auch lange dauern bis zur industriellen Fertigung. Unter anderem, weil das ganze heutige Beschichtungssystem für Stahl geändert werden müsste. Der Nutzen wäre aber riesengroß, ist sich Rohwerder sicher. Die aufwändige und umständliche Wartung von Brücken oder Flugzeugen würde mit intelligenten selbstheilenden Beschichtungen viel weniger Geld verschlingen. Und die Lebensdauer von Stahl würde sich deutlich erhöhen. Was auch dem Klima zugutekäme, denn die CO2-Emissionen bei der Erzeugung von Stahl sind enorm. Hielte das Material länger, müsste weniger neu produziert werden. In punkto Umweltschutz ergäben sich ebenso große Vorteile. „Die meisten hochwirksamen Wirkstoffe gegen Korrosion haben ja eine gewisse chemische Aktivität“, erklärt Rohwerder. Zum Beispiel der effektive Korrosionsbekämpfer Chromat – eine für die Umwelt toxische Substanz, die in Europa weitestgehend verboten ist. Andere Inhibitoren sind ebenfalls ein Umweltproblem oder könnten in Zukunft ein solches werden. Es ist also nie gut, wenn mehr als unbedingt nötig von diesen Substanzen freigesetzt wird. Und da punkten intelligente Beschichtungen. Sie lassen die Wirkstoffe nur bei Korrosion und nur an der betroffenen Stelle frei, was die Menge an Chemikalien, die in die Umwelt gelangen, auf das Nötigste begrenzt. Die Suche nach der Wunder-Beschichtung mag mühsam sein, aber sie lohnt sich auf jeden Fall.
Abbildungshinweise:
Titelbild: © Stefan Alfonso / iStock
Abb. A, B und C: © MPG // HNBM-design.de // CC BY-NC-SA 4.0
Der Text wird unter CC BY-NC-SA 4.0 veröffentlicht.
TECHMAX-Ausgabe 19, aktualisiert im Winter 2022; Autor: Andreas Lorenz-Meyer; Redaktion: Tanja Fendt