Techmax 38: Kunststoffe im Kreislauf
plus Shipping Costs
Vom Abfall zur Ressource
Der Bedarf an Kunststoffen wird sich bis 2050 verdoppeln. Doch noch immer werden über 90% davon aus Erdöl hergestellt – rechnet man den Altkunststoff mit ein. Allein durch die Produktion von Plastik wurden etwa im Jahr 2019 bereits 2,24 Gigatonnen CO2 freigesetzt – so viel wie durch 600 Kohlekraftwerke. Will Europa klimaneutral werden, bedarf es dringend neuer Kunststoffe, die sich ohne Qualitätsverlust in einem geschlossenen Kreislauf aus Produktion und Recycling halten lassen. Dafür entwickelt Manuel Häußler am Max-Planck-Institut für Kolloid- und Grenzflächenforschung einen vielversprechenden Ansatz.
Es begann im Jahr 1907 mit Bakelit. Bald folgten Polyvinylchlorid, Polyamid, Polyethylen, Teflon, Polystyrol, Polyurethan, Polyacrylnitril, Polypropylen und andere. Während die erste Hälfte des 20. Jahrhunderts noch ganz im Zeichen der Entwicklung von Polymeren stand, wuchs nach 1950 deren weltweite Produktion geradezu exponentiell. Rund 414 Millionen Tonnen waren es im Jahr 2023 – Tendenz weiter steigend. Kein Wunder, denn unzählige Produkte für Haushalt, Arbeitswelt und Freizeit wurden durch Kunststoffe erst möglich. Ob in der Medizin, bei Verpackungsmitteln, in Handwerk, Automobilindustrie, Elektronik oder Textilherstellung – kaum ein Bereich, in dem kein Plastik eingesetzt wird. Kein anderes Material ist so leicht, robust, wasserabweisend, vielfältig – und vor allem so preiswert! Je nach chemischer Zusammensetzung können Polymere hart oder weich sein, elastisch, transparent, isolierend, korrosions- und chemikalienbeständig. Holz, Metall, Keramik oder Glas können, was die vielfältige Performance betrifft, bei weitem nicht mithalten.
Das Müllproblem
Durch Verwendung unterschiedlicher Monomere lassen sich die Eigenschaften von Kunststoffen maßschneidern. „Miniatur-LEGO“ nennt es Manuel Häußler. Doch mittlerweile sind die meisten dieser Polymer-Rezepte mehr als 70 Jahre alt. Kann das molekulare Design noch den heutigen Ansprüchen genügen? „Ganz klar nein, denn damals hat man das Recycling nicht mitbedacht“, sagt Häußler. Und so wachsen nicht nur stetig Bedarf und Produktion – sondern auch der Müll. Im Jahr 2023 fielen in Deutschland 5,58 Millionen Tonnen Kunststoffabfälle von gewerblichen und privaten Endverbrauchern an (Abb. A). Das sind fast 66 kg pro Person. 36 kg davon sind nur Verpackungsmüll – etwa die Hälfte des Körpergewichts eines Erwachsenen! Die gute Nachricht: Sehr wenig Plastik landet in Deutschland heute noch auf Deponien. Doch nicht einmal ein Prozent ist Teil eines echten geschlossenen Kreislaufs, ohne jegliche Qualitätsverluste. „Aber genau da müssen wir hin – und zwar mit jeder Art von Kunststoff“, betont Manuel Häußler.
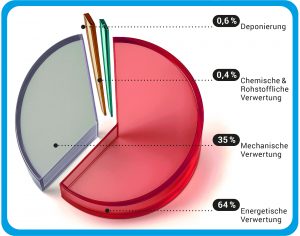
Abb. A: Kunststoffabfälle in Deutschland. Mehr als die Hälfte der Kunststoffabfälle wurde im Jahr 2023 verbrannt – in speziellen Industriekraftwerken als Ersatzbrennstoff oder in Müllverbrennungsanlagen. Mit insgesamt 35,4% stofflicher Verwertung erreichte Deutschland eine der höchsten Raten in Europa.
© Quelle Zahlen: Conversio, Stoffstrombild Kunststoffe in Deutschland 2023, 2024; Grafik: HNBM
Die Krux mit dem Mikroplastik
Polyethylen (PE) ist der am meisten verwendete Kunststoff überhaupt. Durch Zusatz von Prozesshilfen, Farbstoffen oder anderen Additiven lassen sich PE-Produkte in fast beliebiger Konsistenz, Optik und Größe herstellen. HDPE (High Density PE) ist wegen seiner hohen Dichte extrem robust und deshalb ideal für Flaschen, Verschlüsse, Kanister oder Fässer. Die flexiblere LDPE-Variante eignet sich für Folien, Tragetaschen oder Säcke. LDPE (Low Density PE) wird durch radikalische Polymerisation, HDPE durch katalytische Insertionspolymerisation von Ethylen hergestellt. Beide PE-Varianten bestehen jeweils aus sehr langen Kohlenwasserstoffketten (C2H4)n, man könnte sagen, es ist „schnittfestes Erdöl“. Und in diesen Ketten steckt das große Manko von PE. Denn einmal verknäult und im Spritzgussverfahren zu einer Plastiktüte oder -schale geformt, bieten sie Enzymen keinerlei Angriffspunkte, sind deshalb für Mikroorganismen unverdaulich. Gelangt Plastikmüll in die Umwelt, zerfällt er durch Einfluss von UV-Strahlung und Sauerstoff nur unendlich langsam in Mikro- und schließlich Nanoplastik. Aber er bleibt was er war – Plastik.
Zumindest in Deutschland wird Plastikmüll in großen Mengen in gelben Säcken und Tonnen gesammelt. In Sortieranlagen wird er geschreddert und etwa 20 verschiedene Kunststoffsorten können daraus einigermaßen sortenrein getrennt, und neu eingeschmolzen werden. Genau hier liegt aber auch das Problem: Selbst wenn die Sortierung nach Kunststoffsorten perfekt abläuft, so unterscheiden sich die einzelnen Plastikobjekte dennoch in ihrer Additivierung – beispielsweise gibt es erhebliche Unterschiede zwischen PE für technische Anwendungen und Lebensmittelverpackungen. Die Additive und Farbstoffe lassen sich beim mechanischen Recycling nicht abtrennen, aus einer blauen Weichspülerflasche kann also nie mehr eine weiße werden. Hinzu kommt die natürliche Materialalterung, welche die Polymerketten durch UV-Licht und Sauerstoff langsam aber sicher verändert und die Qualität reduziert. „Damit perfekte neue Produkte daraus entstehen, wird das Rezyklat mit viel frisch hergestelltem Kunststoff gemischt, quasi ’verdünnt‘, wofür erneut Erdöl eingesetzt werden muss“, erklärt Häußler. Und das ist keine nachhaltige Lösung. Eine Alternative für das mechanische Recycling ist das chemische Recycling. Dabei werden die Polymerketten wieder zu kleinen Molekülen gespalten, welche sich viel besser auftrennen und reinigen lassen. Das ist bei klassischen Polymeren wie PE aber sehr energieaufwändig: Um die stabilen Polymerketten zu spalten, muss das Material auf bis zu 700 °C erhitzt werden. Dabei entsteht eine komplexe Mischung, sogenanntes Pyrolyseöl, das dem ursprünglichen Erdöl ähnelt, und dadurch erst wieder die petrochemische Aufreinigung durchlaufen muss.
Ein Ersatz für Polyethylen
Manuel Häußler forscht an einem Ersatzstoff für Polyethylen. Sein Ziel: Nur noch einen Monomertyp für viele verschiedene Polymerqualitäten einzusetzen, die sich alle gemeinsam recyceln lassen. Dahinter stehen folgende Überlegungen: Polyethylene ähneln natürlichen Fettsäuren, die typischerweise zwölf oder mehr Kohlenstoffatome besitzen. Oxidiert zu Dicarbonsäuren (DCAs) wären sie perfekt, um etwa mit Diolen durch Polykondensation zu PE-artigen Polymerketten verestert zu werden. Wenn es gelänge, damit vergleichbare Kettenlängen aufzubauen wie beim klassischen PE, müssten auch die Eigenschaften ähnlich sein. Anders als Polyethylen ließen sich diese Kunststoffe aber nach Gebrauch einfach hydrolisieren und die langkettigen kohlenstoffreichen Monomere in den Kreislauf zurückführen. Gedacht, getan: Als Rohstoff setzte Häußlers Team Pflanzenöl ein, das großtechnisch raffiniert wurde, um damit 1,18-Octadecandisäure herzustellen. Aus dieser entsteht durch Veresterung mit einem langkettigen 1,18-Octadecandiol und anschließender Polykondensation der Polyester-18,18 (Abb. B).
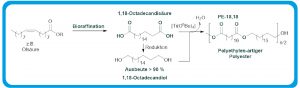
Abb. B: Herstellung von Polyester-18,18. Durch Bioraffination von Pflanzenölen entsteht 1,18-Octadecandicarbonsäure, die teilweise zu 1,18-Octadecandiol reduziert wird. Die Alkohol- und Säureendgruppen der Monomere reagieren unter Veresterung miteinander. Da jedes Molekül zwei Endgruppen besitzt, wiederholt sich die Veresterung vielfach. Diese Polykondensation führt unter Abspaltung von Wasser zur Bildung des Polyesters-18,18.
© M. Häußler, MPI für Kolloid- und Grenzflächenforschung / CC BY-NC-SA 4.0
Der Kunststoff besteht aus cremeweißen Pellets, die sich – typisch für Plastik – vielseitig verarbeiten lassen. Im Spritzgussverfahren und mittels 3D-Druck stellte Häußlers Team daraus unter anderem mechanische Teststäbchen, aber auch komplexere Objekte wie Smartphone-Hüllen oder hitzestabile Espressotassen her. Inzwischen nimmt das Forschungsteam als Rohstoff buchstäblich Müll: Kleingehäckselte, auch minderwertige Kunststoffabfälle und Lebensmittelreste werden oxidiert und dann mithilfe bestimmter Hefen zu langkettigen Dicarbonsäuren fermentiert. Denn die Verwendung von Pflanzenölen ist zwar nachhaltig, aber auch kritisch zu sehen, weil sie als Speiseöle der Welternährung dienen.
Eigenschaften des neuen Polyesters
„Die thermischen und mechanischen Eigenschaften des Polyesters-18,18 sind HDPE verblüffend ähnlich“, sagt Häußler. Speziell, was Verformbarkeit, Zugfestigkeit und Kristallinität angeht (Abb. C). Auch die Kettenlängen sind vergleichbar. „Das Material ist semikristallin und hat 50% bis 70% sich wiederholende, regelmäßige Kristallstrukturen.“ Die Eigenschaften des neuen Materials lassen sich über die Kettenlängen der Monomere gezielt steuern: Je länger die Alkanketten zwischen den Estergruppen, desto robuster wird das spätere Produkt: Es wird kristalliner, steifer, zugfester und auch härter. „Irgendwann, etwas jenseits von C30, verhält es sich wie ein klassisches Polyethylen und die Abbaubarkeit sinkt wieder deutlich“, erklärt der Forscher. Die Kettenlänge muss also gut austariert werden, damit der Nachhaltigkeitsvorteil nicht verloren geht.
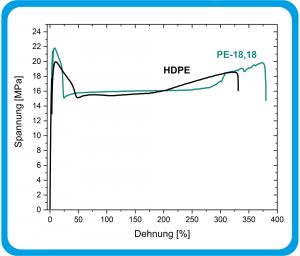
Abb. C: Polymere im Test. Testkörper werden eingespannt und mit einer Kraftmesszelle langsam gestreckt, bis sie reißen. Die dabei aufgenommene Spannungs-Dehnungs-Kurve gibt Aufschlüsse über die Materialbeschaffenheit.
© M. Häußler, MPI für Kolloid- und Grenzflächenforschung / CC BY-NC-SA 4.0
Die Monomere können entweder sortenrein oder in bestimmten Mischungsverhältnissen eingesetzt werden. Ändert man die Verbindungsstellen, etwa indem auch Diamine verwendet werden und damit zufällig die eine oder andere Estergruppe durch eine Amidgruppe ausgetauscht wird, entstehen viele weitere Kombinationsmöglichkeiten. „Wir spielen ganz bewusst mit dem Einbringen von Heteroatomen. Man kann auch die Bildung von Wasserstoffbrücken fördern. Oder Seitenketten als Kristallisations-Brecher mit ins Spiel bringen, wodurch das Material weicher wird“, sagt er Chemiker. Nach Gebrauch könnten diese Kunststoffe prinzipiell in die gelbe Tonne, denn ihre Nah-Infrarotsignatur unterscheidet sich ausreichend von den anderen gut trennbaren Kunststoffen. In Sortieranlagen werden sie nach Schreddern des Plastikmülls von entsprechenden Sensoren erkannt und per Luftstoß aussortiert. „Das wird aber nicht gleich am Anfang passieren“, schätzt Manuel Häußler, „denn es lohnt sich nicht, eine Sortieranlage, durch die pro Jahr 100.000 Tonnen Kunststoff laufen, für anfangs nur wenige Tonnen neuen Kunststoff umzubauen.“ Ein entscheidender Vorteil: Gelangen die neuen Polymere in die Umwelt, kann daraus kein schädliches Mikroplastik entstehen, da sich schnell Biofilme aus verschiedensten Mikroben bilden, deren Enzyme die Ester spalten. Die freigesetzten Monomere werden von Bakterien und Pilzen dann in kurzer Zeit verstoffwechselt, weil die Dicarbonsäuren wie natürliche Fettsäuren abgebaut werden können. Trotzdem will er nicht, dass seine Kunststoffe in die Umwelt gelangen. „Ihr Charme liegt ja darin, dass sie vollständig und ohne Qualitätsverlust recycelbar sind“, sagt der Forscher.
Ein Kunststoff für die Kreislaufwirtschaft
Anders als PE mit seiner reinen Kohlenwasserstoffkette besitzen die langkettigen PE-artigen Polyester klar definierte „Sollbruch stellen“ – die Estergruppen – die das Polymer vollständig rezyklierbar machen. Ein weiterer Vorteil: Es lässt sich unter milden Bedingungen depolymerisieren (Kasten). Farbstoffe und weitere Additive können bei der Depolymerisation auch leicht abgetrennt werden und das Monomergemisch lässt sich im Prinzip sofort erneut verwenden und verestern. „Im Grunde zirkulieren wir zwischen Herstellung und Recycling lediglich ein Äquivalent Wasser: Bei der Esterbildung wird es entzogen – bei der Spaltung verbraucht“, sagt Häußler. Nirgendwo entsteht CO2.
In fünf bis zehn Jahren, denkt Häußler, sollte die neue Kunststoffklasse für Massenanwendungen marktreif sein – für Spezialanwendungen sogar schon viel früher. Den Anfang werden wohl High-Performance-Produkte wie Gegenstände aus dem 3D-Drucker machen. Bei deren Herstellung fällt bislang sehr viel Abfall an, weil die Materialien bei der Verarbeitung stets an Qualität verlieren. Druckerreste der neuen Polyester können hingegen nach dem solvolytischen Recycling ohne Qualitätsverlust wieder zum Drucken verwendet werden. „Auf längere Sicht werden es sicher auch diverse Verpackungsmaterialien oder Haushaltsprodukte sein, die über die Gelbe Tonne gesammelt werden können“, sagt der Chemiker. Aktuell spielen die Forschenden mit den Rezepturen, um die Anwendungsmöglichkeiten des PE-Ersatzes auszuloten (Abb. D).
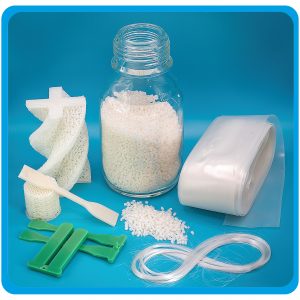
Abb. D: Verschiedene Produkte aus PE-artigem Polyester.
© M. Häußler, MPI für Kolloid- und Grenzflächenforschung
Kunststoffe der Zukunft
Um zukunftsfähig zu sein, müssen neue Kunststoffe aus Häußlers Sicht vier Kriterien erfüllen: „Erstens: Herstellung aus unkritischen Rohstoffen. Zweitens: Vielseitigkeit in der Anwendung. Drittens: Abbaubarkeit in der Umwelt zur Vermeidung von Mikroplastik. Und viertens: vollständige Rezyklierbarkeit.“ Alle bisherigen Ansätze scheitern mindestens an einem Kriterium. Die PE-Alternativen erfüllen hingegen alle Kriterien in einem molekularen Konzept und erreichen dabei die Leistung herkömmlicher Kunststoffe. DCA-basierte Polymere haben das Potenzial für vielfältige High-Performance-Produkte – und damit für eine Plattformtechnologie. „Das ist auch die Voraus-setzung für den Markterfolg. Für tausende Produkte auch tausende verschiedene nachhaltige Polymertypen zu entwickeln, wäre völlig unrentabel“, betont Häußler. Werden wir dann bald in einer PE-freien Welt leben? Manuel Häußler ist vorsichtig: Im Moment seien die bestehenden Produktionskapazitäten für herkömmliche Kunststoffe einfach zu groß. Warum sollte die Industrie sie stilllegen? „Aber vielleicht schaffen wir es bis 2050, zumindest keine neuen erdölbasierten Produktionsanlagen mehr auf zubauen“, sagt er.
Abbildungshinweise:
Titelbild: © HNBM
Abb. A: © Quelle Zahlen: Conversio, Stoffstrombild Kunststoffe in Deutschland 2023, 2024; Grafik: HNBM
Abb. B: © M. Häußler, MPI für Kolloid- und Grenzflächenforschung / CC BY-NC-SA 4.0
Abb. C: © M. Häußler, MPI für Kolloid- und Grenzflächenforschung / CC BY-NC-SA 4.0
Abb. D: © M. Häußler, MPI für Kolloid- und Grenzflächenforschung
Kasten: © M. Häußler, MPI für Kolloid- und Grenzflächenforschung / CC BY-NC-SA 4.0
Der Text wird unter CC BY-NC-SA 4.0 veröffentlicht.
TECHMAX Ausgabe 38, Juli 2025; Text: Dr. Catarina Pietschmann; Redaktion: Dr. Tanja Fendt