Techmax 27: Drucken in drei Dimensionen
plus Shipping Costs
Wie Forscher filigrane Formen aus Metall produzieren
„Jetzt kann man die Minerva schön sehen“, sagt Eric Jägle. Unter dem Fenster des „3D-Druckers“ verschweißt ein hin und her rasender, glühender Laserlichtpunkt feines Metallpulver zum Kopfrelief der antiken Göttin. Es entsteht eine Münze aus Edelstahl mit Logo der Max-Planck-Gesellschaft, als Geschenk für Besucher. Wir befinden uns in einem Labor im Max-Planck-Institut für Eisenforschung in Düsseldorf. Jägle forscht mit seiner Gruppe daran, Metall-Werkstoffe für den „3D-Druck“ zu verbessern. Das ist alles andere als einfach, lernt man bei ihm. Schließlich schmilzt das Metall im Laserfokus bei mehreren Tausend Grad kurz auf und wird praktisch sofort wieder fest. Dabei kann viel schiefgehen. Jede neue Anwendung im „3D-Druck“ von Metallen erfordert deshalb Grundlagenforschung.
Das dreidimensionale (3D) Drucken von Kunststoffen ist längst Alltag. Der nächste Schritt wäre das Drucken von Metallen. Allerdings lässt Eric Jägle, der eine Werkstoffwissenschaftsgruppe leitet, den Traum vom heimischen Metalldrucker gleich platzen. Das schrankgroße Lasergerät kostet schon in der Basisversion 150.000 Euro. „Und wenn man Zusatzwünsche hat, ist man schnell bei einer halben Million Euro“, sagt Jägle.
Trotzdem ist das 3D-Drucken von Metallen keine Zukunftsvision mehr, sondern industrielle Realität. Wer kürzlich eine Krone als Zahnersatz bekam, beißt sehr wahrscheinlich mit einem 3D-gedruckten Metallteil unter der Keramik ins Brötchen. Immer, wenn es um Einzelanfertigungen oder kleine Stückzahlen geht, ist das 3D-Drucken von Metallteilen interessant. Vor allem kann es beliebig kompliziert geformte Werkstücke in einem Durchgang herstellen. Das ist auch ideal für verschachtelte Bauteile, die bislang aus vielen Einzelteilen zusammengeschweißt werden müssen. Anwendungsgebiete sind neben der Medizin die Luft- und Raumfahrt, Kraftwerksturbinen, Motorsport, Ersatzteile für Oldtimer, auch die Bahn nutzt diese Technik.
Gedruckte Raketen-Brennkammern
Da sich beliebige Formen 3D-drucken lassen, wird extremer Leichtbau möglich. Wie bei verästelten Pflanzenstrukturen befindet sich in solchen Leichtbauteilen nur dort Material, wo es Kräfte aufnehmen muss. „Deshalb kommen heute auch zum Beispiel komplette Raketen-Brennkammern für die Raumfahrt aus dem Drucker“, erklärt Jägle. Der Werkstoffwissenschaftler beantwortet zudem die Frage, warum das „3D-Drucken“ hier in Anführungszeichen geschrieben ist. Industrie und Forschung sprechen lieber von „Additiver Fertigung“ als vom Drucken. Es gibt nämlich viele verschiedene Verfahren, computergesteuert dreidimensionale Objekte aus Metall aufzubauen.
Als erstes erklärt Jägle, warum diese Technik „additiv“ heißt, im Gegensatz zu „subtraktiv“. „Subtraktiv ist zum Beispiel die Bildhauerei“, erklärt er, „so wie Michelangelo seinen berühmten David aus einem Marmorblock herausgearbeitet hat.“ In der Industrie entspricht das dem computergesteuerten Herausfräsen eines Teils aus einem Metallblock. Additiv heißt hingegen, dass man etwas hinzufügt statt wegnimmt, also aufbaut. Allerdings trifft das auch auf das Gießen von geschmolzenem Metall in eine Gussform zu, was die Menschen seit der Bronzezeit beherrschen. Also fehlt noch etwas in der Definition. „Das Ganze muss man auch noch computergesteuert machen“, zählt Jägle weiter auf, „und das ohne Werkzeug!“
Bei der Additiven Fertigung geht es also darum, ein im Computer entworfenes, dreidimensionales Teil möglichst formgetreu aus einem Material aufzubauen. Sie soll vollkommen flexibel beliebige Formen produzieren können. Heute gibt es verschiedene additive Techniken für Metalle, die unterschiedlich weit entwickelt sind. Am weitesten verbreitet sind die sogenannten Pulverbett-Verfahren, bei denen ein starker Infrarotlaser oder ein Elektronenstrahl Metallpulver verschweißt. Der Laserdrucker im Düsseldorfer Labor gehört dazu.
Das Prinzip ist einfach zu verstehen. Als Baumaterial dient feines Metallpulver, weshalb dieses Verfahren Laser Powder Bed Fusion, kurz L-PBF, heißt—also auf Deutsch Laser-Pulverbett-Schmelzen. Das Pulver erzwingt strenge Sicherheitsvorkehrungen, wenn der Drucker geöffnet wird. Schließlich kann das Pulver, wenn es sich als Staubwolke in der Luft verteilt, explodieren. Ursache ist die riesige Gesamtoberfläche aller Metallpartikel zusammengenommen, die im Kontakt mit dem Sauerstoff der Luft schlagartig oxidieren kann. Außerdem ist das Einatmen gefährlich. Deshalb darf man den Drucker nur öffnen, wenn man Schutzanzug und Atemmaske trägt, und man muss sehr sauber arbeiten.
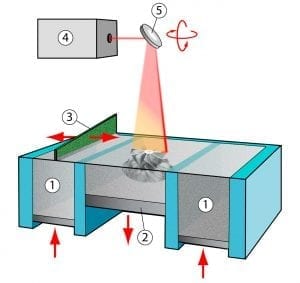
Abb. A: Bei der L-PBF-Technik des 3D-Druckens von Metall verschweißt ein Laserstrahl feines Metallpulver zu einem Bauteil. Links und rechts von dem Volumen, in dem das Bauteil heranwächst, befinden sich Behälter für das Metallpulver (1). Schicht für Schicht fährt der Hubtisch (2) unter dem oben wachsenden Bauteil nach unten. Jedes Mal streicht ein Schieber oder eine Bürste (3) eine neue Pulverschicht aus einem der beiden Reservoirs über das Werkstück. Danach schweißt der Laser (4) über einen computergesteuerten Scannerspiegel (5) die für diese Schicht nötige Form auf.
© R. Wengenmayr / CC BY-NC-SA 4.0
Bauteil aus dem Pulverbett
Das L-PBF-Verfahren, bietet zwei Vorteile. Erstens kann es besonders feine Strukturen herstellen. Zweitens sind die damit gedruckten Metallteile enorm fest. Ihre Festigkeit entspricht der höchsten Qualitätsstufe, dem Schmiedestück. Metalle bestehen aus feinen Körnern, und das Schmieden presst diese besonders dicht und fest zusammen. Ein Schmiedestück ist damit viel zäher und härter als ein Gussteil.
Im L-PBF-Drucker befindet sich das Metallpulver in einem Pulverbett (Abb. A). Eine Schutzatmosphäre aus dem Edelgas Argon verhindert die Oxidation beim Verschweißen. Im ersten Schritt schiebt eine Bürste eine sehr dünne Schicht Pulver über eine Grundplatte. Dann schweißt der Laser die erste Schicht des Bauteils ins Pulver (Abb. B). Sein Strahl wird dafür von einem extrem schnell und präzise gesteuerten Scannerspiegel umgelenkt. Im Lichtfokus fährt ein kleines mobiles Bad aus geschmolzenem Metall durch das Pulver, das außerhalb des Fokus schlagartig abkühlt und fest wird. Ist eine Schicht fertig, fährt ein Hubtisch unter der Platte das Bauteil um exakt eine Schichthöhe nach unten, und die Prozedur wiederholt sich. Es gibt auch Geräte, die mit mehreren Laserstrahlen arbeiten, um schneller zu sein.
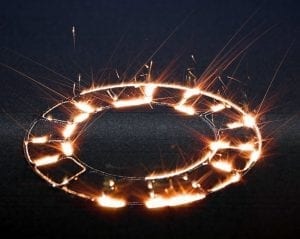
Abb. B: Der rasende Laserstrahl schweißt die neue Schicht eines Bauteils ins Metallpulver.
© Foto: Fraunhofer ILT Aachen / Volker Lannert
Die Höhe einer Schicht hängt davon ab, wie fein die Details sein sollen. Typisch sind zwanzig bis vierzig Mikrometer (Tausendstel Millimeter), was grob dem Durchmesser eines feinen Kopfhaars entspricht. Ein Werkstück kann so aus einigen Tausend Schichten aufgebaut sein. Der Laserstrahl bewegt sich wie ein Stift beim Schraffieren einer Fläche. Deshalb kann ein Bauteil am Ende aus mehreren Millionen kurzer Schweißbahnen mit vielen Kilometern Gesamtlänge bestehen. Wenn das Teil fertig ist, muss es aus dem Pulver herausgeholt, gereinigt (Abb. C) und von der Grundplatte abgetrennt werden.
Der Werkstoffwissenschaftler Jägle interessiert sich für die Vorgänge, die dabei tief im Inneren der geschmolzenen und wieder erstarrten Metalle ablaufen. Das ist Grundlagenforschung, also genau die Max-Planck-Welt. Deshalb sieht das, was Jägles Gruppe druckt, auch nicht so cool aus wie viele Beispiele im Netz. „Wir drucken Würfel“, sagt Jägle und lacht: „Die schneiden wir auseinander und untersuchen sie.“
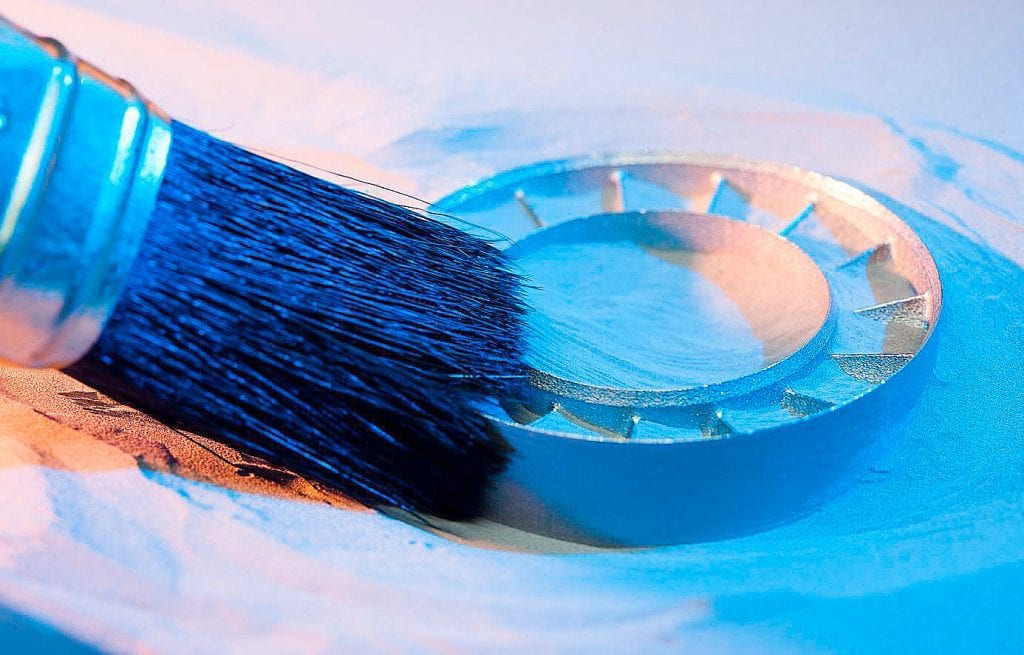
Abb. C: Das fertige Bauteil wird aus dem Metallpulver herausgeholt.
© Foto: Fraunhofer ILT Aachen / Volker Lannert
Schwierige Metall-Legierungen
Beim Einsatz von Metalllegierungen in der Additiven Fertigung können nämlich viele grundlegende Probleme auftreten, und die wollen die Werkstoffwissenschaftler verstehen. Metallische Legierungen bestehen aus mindestens zwei chemischen Elementen, damit sie die gewünschten Eigenschaften bekommen. Die verschiedenen chemischen Elemente in einer Legierung reagieren aber auch unterschiedlich, wenn diese verflüssigt wird. Das erinnert an eine Schokolade, die einmal angeschmol-zen wurde und danach nicht mehr so schön cremig-zart auf der Zunge zergeht: Das Erhitzen hat ihre „Mikrostruktur“ verändert.
Jägle zählt die beim 3D-Drucken von Metalllegierungen auftretenden Probleme auf: „Manche Materialien lassen sich gar nicht verarbeiten, andere sind voller Risse. Manche kommen zwar als Festkörper aus dem Pulverbett, sind aber sehr spröde.“ Einige 3D-gedruckte Werkstoffe ermüden bei mechanischer Belastung viel schneller als sie sollten. In der Hitze des Laserfokus können auch flüchtigere chemische Elemente aus der Legierung verdampfen, was deren Eigenschaften verschlechtert. Es kann zudem passieren, dass ein gedrucktes Werkstück in einer Zugrichtung fester ist als senkrecht zu dieser Richtung.
Eric Jägles Forschungsgruppe untersucht deshalb ihre gedruckten Würfel mit ausgeklügelten Methoden. Sie wollen damit enträtseln, was bei dem Aufschmelzen des Pulvers und anschließenden Erstarren zum Metallteil auf der mikroskopischen Skala passiert. Darauf sind die Düsseldorfer spezialisiert, und die Industrie ist an dieser Grundlagenforschung stark interessiert.
Risse in der Superlegierung
Jägle erzählt von einem aktuellen Forschungsprojekt, an dem mehrere größere und kleinere Unternehmen und verschiedene Universitäten und Forschungsinstitute beteiligt sind. Auch das Max-Planck-Institut für Eisenforschung ist dabei. „Warum kommen bestimmte Nickel-Basis-Superlegierungen mit Rissen aus dem L-PBF-Prozess heraus?“, schildert Jägle die Fragestellung des Projekts. Solche Speziallegierungen werden für Turbinenschaufeln in Kraftwerken, Hubschraubern oder Flugzeugen verwendet. Beim Betrieb können diese Schaufeln über Tausend Grad Celsius heiß werden. Das dann fast weißglühende Metall darf aber nicht ermüden oder korrodieren. Genau das leisten Nickel-Basis-Superlegierungen.
Hinzu kommt, dass diese Turbinenschaufeln durch feine Kanäle gekühlt werden. Deshalb erfordert die Herstellung aufwändige Gießformen. Sie mit den Kanälen in einem Stück drucken zu können, wäre also attraktiv. Das wäre nicht nur billiger, man könnte die Schaufeln nach Bedarf drucken, auch als Ersatzteile.
„Deshalb nehmen mehrere Firmen Millionen in die Hand, um das spannenden Projekt zu finanzieren“, erzählt Jägle: „Ziel ist die Entwicklung einer neuen Legierung, die dieses Rissproblem nicht mehr hat.“ Solche Nickel-Basis-Superlegierungen werden in einer komplizierten Rezeptur mit bis zu 15 chemischen Elementen zusammengemixt und dann in speziellen Schmelzverfahren hergestellt. Grob die Hälfte der Mixtur entfällt auf Nickel, hinzu kommen Chrom, Kohlenstoff, Molybdän, Niob, Titan, Aluminium und weitere Elemente. Jedes Element hat eine bestimmte Funktion im Werkstoff.
Um das Entstehen der feinen Risse verständlich zu machen, erklärt Jägle, wie eine Metalllegierung unter einem Lichtmikroskop aussieht. Wenn man sie poliert und mit einer Säure anätzt, dann sieht man so etwas wie metallisch glänzende Körner (Abb. D). „Das sind Kristalle“, erklärt der Forscher, „und dass Metalle aus Kristallen bestehen, ist für viele eine Überraschung, schließlich denkt man erst mal an so etwas wie Diamant oder Bergkristall“.
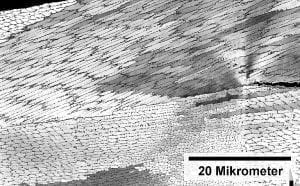
Abb. D: Das Elektronenmikroskopbild zeigt die polierte und angeätzte Oberfläche einer Nickel-Legierung. Die Kristallkörner sind gut erkennbar.
© MPI für Eisenforschung
In der Regel sind die Kristalle mikroskopisch klein, in additiv gefertigten Legierungen sogar extrem fein. Typisch sind dann Abmessungen von einigen Hundert Nanometern (Milliardstel Meter). Sind die Legierungen so komplex wie eine Nickel-Basis-Superlegierung, dann sind die einzelnen Kristalle auch chemisch unterschiedlich zusammengesetzt. Das erinnert entfernt an ein Körnerbrot, in dessen Teig verschiedene Körnersorten stecken. Kühlt eine solche Legierung außerdem aus der Schmelze ab und geht in den festen Zustand über, dann werden ihre chemischen Bestandteile auch nicht alle zur gleichen Zeit fest. Für einen gewissen Moment des Abkühlens überzieht ein hauchdünner Flüssigkeitsfilm die Oberflächen der schon fest gewordenen Kristallkörner.
Überflüssige Übeltäter
Und dieser dünne Flüssigkeitsfilm kurz vor dem Erstarren ist der Übeltäter, der die Risse verursacht. Wenn die Kristallkörner abkühlen, schrumpfen sie nämlich. Metalle reagieren auf Temperaturänderungen durch relativ starkes Ausdehnen oder Zusammenziehen. Solange sich zwischen den Körnern in der Legierung flüssiges Material befindet, kann ein schrumpfendes Korn an seiner Kontaktfläche zum Nachbarkorn abreißen. Beim weiteren Schrumpfen klafft dann an dieser Stelle ein Riss auf (Abb. E). Das Forschungsziel der Düsseldorfer ist deshalb eine kleine, aber wirksame Änderung in der Rezeptur. Sie soll in Zukunft diesen schädlichen Flüssigkeitsfilm beim Abkühlen verhindern.
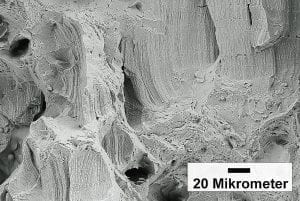
Abb. E: Das Elektronenmikroskopbild zeigt die Bruchstelle eines 3D-gedruckten Werkstücks aus einer Nickel-Legierung. Die dunklen Löcher sind unerwünschte Risse, die das Bauteil schwächen.
© MPI für Eisenforschung
Allerdings würde es viel zu lange dauern, wenn Jägles Forschungsgruppe einfach herumprobieren würde. Mit einer Mischung aus Erfahrung, Computerprogrammen und der genauen Analyse der zersägten Würfel versuchen die Forscher, die beste Rezeptur möglichst effizient aufzuspüren. Eine Spezialität des Max-Planck-Instituts für Eisenforschung sind sogenannte Atomsonden. Wie diese funktionieren, erklärt der TECHMAX 19. Damit können die Forscher im Extremfall bis auf Atome genau entschlüsseln, wie die Körner des gedruckten Materials räumlich aufgebaut sind.
An der Additiven Fertigung fasziniert, wie eng die Grundlagenforschung mit der industriellen Anwendung verknüpft ist. Jägle zitiert eine berühmte Feststellung von Max Planck, dem Namensgeber der Max-Planck-Gesellschaft: „Dem Anwenden muss das Erkennen vorausgehen.“ Das klingt fast so, als hätte Planck schon vor Jahrzehnten die Welt des 3D-Druckens vorausgesehen.
Abbildungshinweise:
Titelbild: Symbolbild © GE Additive
Abb. A: LPBF-Technik © R. Wengenmayr / CC BY-NC-SA 4.0
Abb. B und C © Fraunhofer ILT Aachen / Volker Lannert
Abb. D und E © MPI für Eisenforschung
Der Text wird unter CC BY-NC-SA 4.0 veröffentlicht.
Die vorgestellte Forschung wird nicht von General Electric gefördert.
TECHMAX Ausgabe 27, Frühjahr 2020; Autor: Roland Wengenmayr; Redaktion: Tanja Fendt