Techmax 25: Mikroplastik im Meer
plus Shipping Costs
Warum Chemiker nach bioabbaubaren Kunststoffen forschen
Die Geschichte der Menschheit lässt sich nach ihren Werkstoffen in Epochen einteilen: Steinzeit, Bronzezeit, Eisenzeit. Die Epoche ab Mitte des 20. Jahrhunderts könnte als Plastikzeitalter in die Geschichte eingehen. Wir müssen nur einen Tag lang aufmerksam beobachten, wo uns Kunststoffe begegnen. Sie sind überall: in der Kleidung, in Brillen, Fenstern, Türen und Isolationen von Häusern, in elektronischen Geräten, Fahrzeugen und Verpackungen aller Art. Wir leben ganz offensichtlich im Plastikzeitalter. Kunststoffe sind einerseits ein Segen. Als geniale, leichte, verformbare und energiesparende Alleskönner erleichtern sie uns unser Leben. Auf der anderen Seite sind sie zu einem Problem geworden − wegen ihrer Haltbarkeit. Beim Urlaub am Meer schwappt einem das Plastikzeitalter geradezu entgegen: Auf den Stränden liegen angespülte Flaschen, Tüten, Plastikfetzen. Auf einigen Ozeanen schwimmen große „Plastikinseln“. Und der Nordatlantik wird zunehmend zur „Plastiksuppe“, die starke Strömungen permanent durchmischen.
Ein großer Anteil des Plastikmülls entfällt auf feine Mikropartikel aus Kunststoff. Dieses „Mikroplastik“ mit einer Größe von einigen Mikrometern – also Millionstel Meter – entsteht zum Teil durch Zerfall größerer Plastikteile. Andere Quellen sind verlorengegangenes Plastikgranulat, das Rohmaterial der Kunststoffindustrie, sowie feine „Schleifpartikel“ aus Kosmetika wie Zahnpasta oder Peelingcremes. Schweden zieht nun die Konsequenzen und verbietet zum 1. Juli 2018 den Verkauf solcher Kosmetikprodukte. Viel Mikroplastik wird etwa auch aus Funktionskleidung frei, die in Waschmaschinen durchgewalkt wird oder beim Abrieb von Reifen, den Regen durch die Kanalisation ins Abwasser spült. Da Kläranlagen Mikroplastik nicht völlig aus dem Wasser entfernen können, gelangt einiges davon in Flüsse und schließlich Ozeane.
Nach Untersuchungen der internationalen Naturschutzorganisation IUCN werden jedes Jahr zwischen 0,8 und 2,5 Millionen Tonnen Kunststoff-Mikropartikel in die Ozeane gespült. Und amerikanische Forscher der Universität Georgia haben herausgefunden, dass die Menge an Plastikmüll jeder Art weltweit jährlich um 4,8 bis 12,7 Millionen Tonnen anwächst. Angesichts solcher Zahlen wird klar, dass wir Menschen unseren Planeten auch mit Kunststoffen verändern. Plötzlich taucht überall ein Material auf, das es in der Erdgeschichte zuvor nicht gab. Es ist also höchste Zeit, die möglichen Folgen genauer zu erforschen. Von zerkleinerten Plastikteilen wissen wir, dass Meeresschildkröten und viele Seevögel sehr darunter leiden. Sie verwechseln diese mit Nahrung und müssen dann verhungern, weil der unverdauliche Müll ihre Mägen verstopft.
„Bei den Kunststoff-Mikropartikeln dagegen ist noch nicht klar, inwieweit sie für Menschen und Tiere gefährlich sind“, erklärt Frederik Wurm. Es könnte gut sein, dass das Mikroplastik einfach wie Sand durch die Verdauungsorgane von Organismen hindurchwandert, ohne Schaden anzurichten. Frederik Wurm ist Chemiker und leitet die Gruppe „Funktionelle Polymere“ am Max-Planck-Institut für Polymerforschung in Mainz. Mit einem Teil seines Teams macht er im Forschungsprojekt PlastX mit, das vom Bundesforschungsministerium gefördert wird. Auch die Verbraucherzentrale Nordrhein-Westfalen, die Gesellschaft für Internationale Zusammenarbeit und die Supermarktkette Tegut unterstützen PlastX. Das zeigt schon, wie viele verschiedene Lebensbereiche das Thema Plastikmüll betrifft. Deshalb sind an PlastX auch unterschiedliche Forschungsrichtungen beteiligt: Sozioökonomen von der Goethe Universität Frankfurt untersuchen das Konsumverhalten der Menschen. Sie versuchen Wege aufzuzeigen, wie man das Wegwerfverhalten ändern könnte. Gerade in ärmeren Gesellschaften ist das „wilde Entsorgen“ ein Problem. Ökotoxikologen erforschen, ob Mikroplastik für Organismen schädlich sein könnte. „Derzeit füttern sie Daphnien, kleine Wasserflöhe, damit und schauen, ob ihnen das schadet“, erzählt Wurm. Er ist begeistert von der engen Zusammenarbeit mit Kolleginnen und Kollegen aus verschiedenen wissenschaftlichen Disziplinen.
Bioplastik wird in der Natur nicht abgebaut
Die Mainzer Chemiker entwickeln Ideen für neue Kunststoffe, die in der Umwelt abbaubar sind. Ihre Materialproben werden dann auch von den Frankfurtern an Wasserflöhen getestet. Allerdings ist die Herausforderung der biologischen Abbaubarkeit viel komplizierter, als Wurm anfangs dachte. Was heute zum Beispiel als „Biokunststoff“ vermarktet wird, ist nämlich nicht „bio“, wenn es unkontrolliert in die Umwelt gelangt. Nur bei den hohen Temperaturen, die in industriellen Kompostierungsanlagen herrschen, zersetzen sich solche Kunststoffe. „Der heute von der Werbung verwendete Begriff Bioplastik ist also eigentlich irreführend“, sagt Wurm.
Aber was sind Kunststoffe, chemisch gesehen? Es sind sogenannte Polymere, lange Ketten, die aus vielen kleineren, immer gleichen Molekülbausteinen bestehen. Diese Bausteine heißen Monomere. Ein Kunststoff enthält aber noch verschiedene Zusätze, „Additive“, etwa Farbstoffe. Die beiden aus Umweltsicht wichtigsten Additive sind Weichmacher und Flammschutzmittel. Weichmacher machen, wie der Name schon sagt, die Kunststoffe erst flexibel, sodass sie sich etwa zu Folien verarbeiten lassen. In reiner Form sind viele Polymere eher spröde, hart und in Teilen sogar kristallin.
Da die meisten Kunststoffe brennbar sind, enthalten sie Flammschutzmittel. Diese Substanzen machen je nach Kunststoff bis zu fünfzig Prozent seines Gewichts aus. „Das sind meist Organophosphate, auch Phosphorsäureester genannt, und Halogenkohlenwasserstoffe“, erklärt Wurm: „Und die sind potenziell giftig.“ Solche Flammschutzmittel sind für die Mainzer ein wichtiges Forschungsgebiet, denn sie sind spezialisiert auf Phosphorchemie. Derzeit forschen sie auch an alternativen Phosphorverbindungen, die als Flammschutzmittel biologisch abbaubar und möglichst unbedenklich sind.
Die Kunststoffsorten, die weltweit am meisten verwendet werden, basieren auf dem enorm vielseitigen Polyethylen (PE). „Davon werden ungefähr hundert Millionen Tonnen pro Jahr produziert“, sagt Wurm. Aus PE werden vor allem Verpackungen gemacht, aber auch viele andere Dinge, etwa Wasserrohre oder Teile für Gelenkprothesen. Wie der Name schon sagt, sind im Polyethylen viele Ethen-Monomere miteinander zu langen Ketten verbunden. Ethen wurde früher Ethylen genannt. Herstellen lässt es sich zum Beispiel aus Ethan, dem Hauptbestandteil von Erdgas. Das Ethen-Molekül besteht aus zwei Kohlenstoffatomen (C) und vier Wasserstoffatomen (H), wobei die beiden Kohlenstoffatome über eine Doppelbindung fest zusammenhalten. Das ergibt die chemische Formel H2C=CH2 für ein Ethen-Monomer. Die chemische Reaktion beim Polymerisieren bricht nun diese Doppelbindung auf. Sie verknüpft über die freiwerdenden zwei Einzelbindungen wie mit Steckern die benachbarten Monomere. Wichtig sind dabei Katalysatoren als Reaktionsbeschleuniger. Das entstehende Polymer schreibt sich einfach als (–CH2–CH2–)n, wobei n für die Anzahl der Monomere steht. Je größer n ist, desto länger ist die Kette, was die Eigenschaften des Kunststoffs festlegt.
Ein einziges Monomer bildet ein süßlich riechendes, entzündliches Gas. Aus kurzen Ketten mit wenigen Monomeren entstehen Paraffine, also künstliche Öle und Wachse. Wachs schmilzt leicht. Je länger die PE-Molekülkette wird, desto höher steigt die Schmelztemperatur des Kunststoffs an. Und seine Festigkeit wächst: Eine Kette mit einigen tausend Monomeren eignet sich für Plastiktüten und eine mit hunderttausend Monomeren sogar für schusssichere Westen (Abb. A). PE hat also tolle Eigenschaften für viele Anwendungen. Leider ist es biologisch nicht abbaubar.
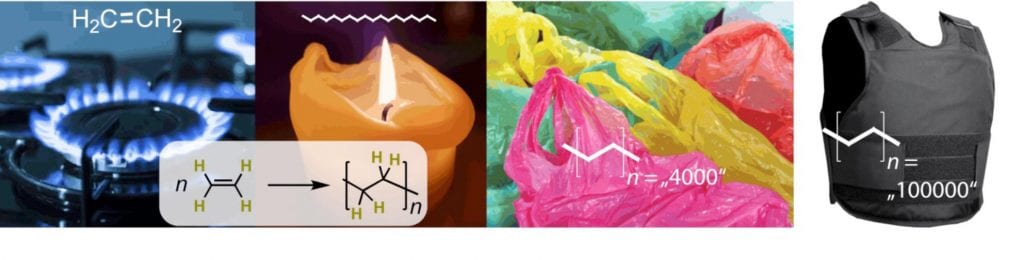
Abb. A: Die Länge der Polymerketten bestimmt die Eigenschaften des Materials. Einzelne Ethen-Moleküle bilden ein Gas, Ethen kann aus Erdgas gewonnen werden (li.). Eine Kette aus wenigen Ethen-Monomeren bildet Paraffin (Kerze in der Mitte). Das Paraffin-Molekül ist oben im Bild in einer vereinfachten Zickzack-Darstellung gezeigt, an jedem Knick sitzt ein CH2. Je länger die PE-Ketten werden, desto stabiler ist das Material, bis es sich sogar für schusssichere Westen eignet (re.). Die Zahlenwerte für n sind nur ungefähre Angaben. Links unten: Polymerisationsreaktion von n Ethen-Molekülen (li.) zu Polyethylen (PE, re.).
© R. Wengenmayr
Als Wurm mit seiner Gruppe anfing, im Rahmen des PlastX-Projekts nach Alternativen für Polyethylen zu forschen, schien das Ziel einfach zu sein. Sie kannten sich sehr gut in der Chemie der Phosphorverbindungen aus. Mit diesem Wissen sollten sie elegant bioabbaubare Kunststoffe entwickeln können. „Phosphor ist faszinierend“, meint Wurm, „zum Beispiel sorgt es für die Stabilität von DNS-Molekülen, in denen die genetische Information einer jeden Zelle steckt.“ Auf der anderen Seite kann man Phosphor in Form von Phosphatmolekülen als gezielte Schwachstellen in Polymerketten einbauen. An diesen Stellen könnten dann zum Beispiel Mikroben chemisch „knabbern“ und so allmählich die Ketten zerlegen. Der Kunststoff wäre biologisch abbaubar.
Chemische Angriffspunkte für Mikroben
Das war der Plan, mit dem die Mainzer starteten. Doch inzwischen ist klar, dass das nicht so einfach ist. Ein Joghurtbecher etwa darf sich nicht schon im Kühlschrank zersetzen. Das verwendete Polymer muss so konstruiert sein, dass das Zersetzen erst nach der Benutzung beginnt. „Für trockene Produkte wie Mehl oder Salz ist das einfacher“, sagt der Chemiker, „für alles, was feucht oder fetthaltig ist, ist es extrem schwierig, einen funktionierenden Kunststoff zu entwickeln.“ Außerdem müssen die Polymerketten beim Abbau auch an den richtigen Stellen zerlegt werden. Es sollen ja keine kleineren Moleküle entstehen, die dann umweltschädlich sind.
Von der komplexen Herausforderung ließen sich die Mainzer aber nicht abschrecken, und tatsächlich gelangen inzwischen erste Schritte zu einem „Biopolyethylen“. Dazu synthetisieren sie im Labor zunächst ein spezielles Monomer. Dabei handelt es sich eigentlich schon um eine kurze Polymerkette, in deren Mitte eine Phosphatbrücke eingebaut ist. Das soll die zukünftige Schwachstelle sein. Nun verwenden die Forscher eine Art von Reaktion, die Alkenmetathese heißt. Alkene zeichnen sich durch mindestens eine Kohlenstoff-Doppelbindung aus; Ethen ist ein Alken. Die Alkenmetathese zerschneidet die Kohlenstoff-Doppelbindungen, platziert Alken-Stücke in den entstehenden Molekülen um und bildet neue Kohlenstoff-Doppelbindungen. Dieses chemische Vertauschungsspiel nutzen die Wissenschaftler, um ihr Polymer im Reagenzglas herzustellen (Abb. B).
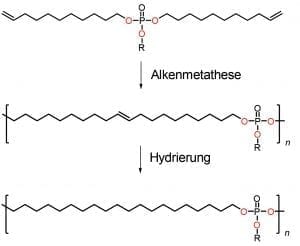
Abb. B: Synthese eines Mainzer „Biopolyethylens“. Oben ist das Monomer mit dem eingebauten Phosphat in der Mitte zu sehen (P steht für Phosphor, O für Sauerstoff, R für einen Molekülrest, der hier nicht wichtig ist). Bei der Alkenmetathese werden aus vielen Monomeren lange Polymerketten (Mitte); n steht für die Anzahl der Monomere. Das nun entstandene Polymer enthält noch eine Doppelbindung. Der nächste Schritt – die sog. Hydrierung – erzeugt durch das Anbinden von Wasserstoffatomen das abbaubare Polyethylen.
© F. Wurm, MPI für Polymerforschung / CC BY-NC-SA 4.0
Im Labor zeigt Doktorand Hisaschi Tee ein kleines gläsernes Reaktorgefäß. „Dort kommt das Monomer rein, dann geben wir den Katalysator hinterher“, erklärt Wurm. Um die Alkenmetathese richtig in Schwung zu bringen, erwärmen die Chemiker den Reaktor schrittweise auf 60 bis 80 Grad Celsius. Ein Rührer durchmischt die Flüssigkeit. Der Katalysator, der die Reaktion beschleunigt, ist ein sogenannter Grubbs-Katalysator. Solche Katalysatoren haben Alkenmetathesen erst richtig erfolgreich gemacht. Benannt sind sie nach dem amerikanischen Chemiker Robert Grubbs, der dafür 2005 den Nobelpreis für Chemie erhielt.
Polymere wie Polyethylen besitzen eine weitere Eigenschaft, die im Plan der Max-Planck-Forscher eine entscheidende Rolle spielt. Ihre langen Molekülketten legen sich gerne streckenweise in gleichmäßigen Schlaufen zusammen. Sie bilden so hochgeordnete Bereiche des Polymers, die kristallin sind. Die harten „Kristallite“ sind über ungeordnete, aber miteinander verschlaufte Abschnitte verbunden. Diese Brücken zwischen den Kristalliten sind auch für die mechanischen Eigenschaften des Kunststoffs verantwortlich. In den ultralangen Ketten des besonders zähen PE-Kunststoffs für schusssichere Westen sind vor allem sie für das Stoppen einer Kugel verantwortlich. Die stabilen Kristallite verhindern den biologischen Abbau, weil Mikroorganismen sie nicht „anbeißen“ können.
Bei dem Mainzer „Biopolyethylen“ falten sich nun die Schlaufen gerade so, dass sich die Phosphate wegen ihres Platzbedarfs ganz außen auf den Kristallen anordnen (Abb. C). Dort kommen Mikroorganismen gut an diese Schwachstellen heran und können die Kristalle biochemisch anknabbern. Die Kristalle zerfallen und das Polymer zersetzt sich.
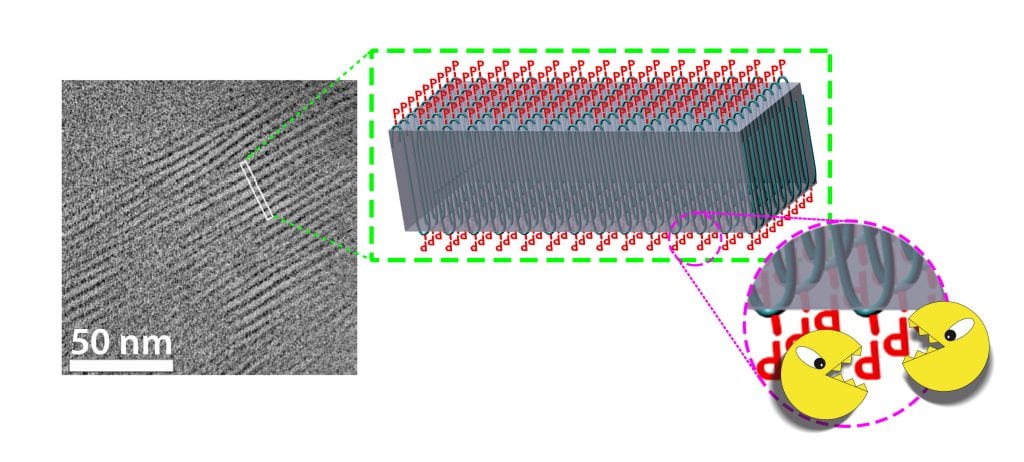
Abb. C: Elektronenmikroskopisches Bild eines Mainzer „Biopolymerkristalls“. Das kleine rechteckige Feld (li.) zeigt einen Ausschnitt aus einer elektronenmikroskopischen Aufnahme. In der Mitte ist dieser Ausschnitt vergrößert als Grafik im Schnittbild dargestellt. Man erkennt die Schlaufen des Polymers im Kristall. Außen an den Knicken sitzen die Phosphate (rotes P) als eingebaute Schwachstellen. An diesen sollen Mikroorganismen beim biologischen Abbau „knabbern“ können, sodass sich die Schlaufen auflösen (re.).
© F. Wurm, R. Wengenmayr / CC BY-NC-SA 4.0
Die ersten Versuche der Mainzer endeten bei einem eher wachsartigen Material. Die Polymerketten waren noch arg kurz. Doch inzwischen gelingen im Labor so lange Ketten, dass sich das Material zu Folien verarbeiten lässt. „Das machen wir wie beim Crêpe“, sagt Wurm: „Wir streichen es mit einem kleinen Abstreichholz aus und lassen es trocknen.“ Im Labor zeigt Hisaschi Tee, wie die Mainzer erst einmal mit Chemikalien wie Natronlauge prüfen, ob und wie die neuen Polymerfolien sich zersetzen. Das Ergebnis untersuchen sie mit Methoden, die ihnen genaue Informationen über die chemischen Strukturen der Polymerbruchstücke liefern.
Sieht das Resultat ermutigend aus, dann kommt der Test mit lebenden Organismen dran. Neben den Wasserflöhen in Frankfurt testen die Mainzer das auch selbst mit Mikroben, zum Beispiel aus Meerwasser oder Belebtschlamm aus Kläranlagen. Dazu verwenden sie spezielle Glasflaschen, sogenannte OxiTop-Systeme. Diese füllen sie mit dem Wasser oder Schlamm und geben Proben ihres neuen Kunststoffs hinzu. Dann lagern sie die Flaschen 28 Tage lang bei konstanter Temperatur. Oben auf der Flasche befindet sich ein Messkopf, der den Druck misst. Wenn die Mikroben den Kunststoff „verdauen“, dann produzieren sie Gase, und das registriert die Druckmessung. Daraus können die Chemiker errechnen, wie schnell sich der Kunststoff in einer bestimmten natürlichen Umgebung biologisch zersetzt.
Die neuen Kunststoffe aus den Mainzer Laboren werden sicher zu teuer für die Massenproduktion sein. Vor allem die Grubbs-Katalysatoren sind zu wertvoll, weil sie Ruthenium benötigen. Doch die Ergebnisse aus Mainz könnten günstige abbaubare Kunststoffe hervorbringen. Schließlich hatten die heutigen Kunststoffe auch einen schwierigen Start. Erst als Karl Ziegler, damals Direktor am Max-Planck-Institut für Kohlenforschung in Mülheim, 1953 mit seinem Team zufällig neue Katalysatoren entdeckte (nach ihren Entdeckern als Ziegler-Natta-Katalysatoren benannt), wurden Kunststoffe im großen Stil industriell herstellbar. Ziegler erhielt dafür 1963 den Nobelpreis für Chemie. Damals setzten Max-Planck-Forscher die Kunststoffe in unsere Welt. Vielleicht gelingt es heute Max-Planck-Forschern, diese revolutionäre Erfindung nachhaltiger zu machen.
Abbildungshinweise
Titelbild: Mikroplastik © Valeria Hidalgo-Ruz, GAME 2013, GEOMAR
Abb. A: Polymerketten © R. Wengenmayr
Abb. B: Synthese-Biopolymer © F. Wurm, MPI für Polymerforschung / CC BY-NC-SA 4.0
Abb. C: Biopolymer-Kristall © F. Wurm, R. Wengenmayr / CC BY-NC-SA 4.0
Der Text wird unter CC BY-NC-SA 4.0 veröffentlicht.
TECHMAX Ausgabe 25, Frühjahr 2018, Redaktion: Christina Beck, Autor: Roland Wengenmayr